18% weniger Energieverbrauch mit Kompaktspinnmaschine K 48
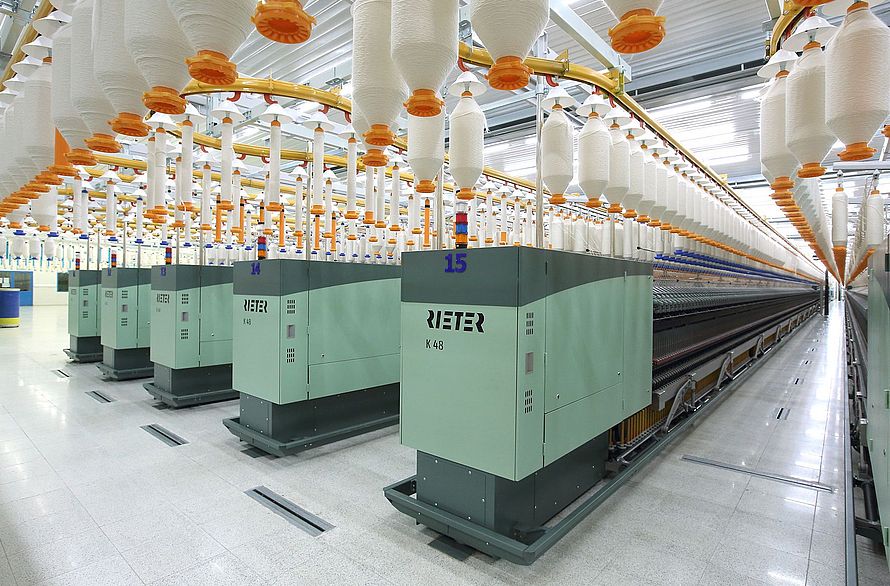
Ein kürzlicher Vergleich in einer türkischen Spinnerei ergab einen um 18% niedrigeren Energieverbrauch der Kompaktspinnmaschine K 48 im Vergleich zum Wettbewerber. Bei einer Maschine mit 1 824 Spindeln entspricht dieser Vorteil einer jährlichen Ersparnis von rund 12 000 USD pro Maschine. Somit bestätigte sich erneut, dass die Kompaktgarntechnologie von Rieter den weltweiten Massstab in Sachen Energienutzeffekt setzt. Diese Ergebnisse sind nicht nur von wesentlicher Bedeutung für den Erfolg von Rieter und seinen Kunden, sondern leisten auch einen Beitrag zu einer nachhaltigeren und wirtschaftlicheren Zukunft der Textilindustrie.
Die Versuche beim Kunden in der Türkei wurden auf Kompaktspinnmaschinen durchgeführt. Dabei kam eine Spindeldrehzahl von 19 200 U/min für die Produktion von 100%igem Baumwollkompaktgarn Ne 30 zur Anwendung. Der Energieverbrauch in kWh pro kg Garn ist eine der wichtigsten Kennzahlen in Spinnereien. Mit 1.21 kWh/kg für die K 48 im Vergleich zu 1.48 kWh/kg für die Wettbewerbermaschine ist der Vorteil der K 48 klar erkennbar. Dadurch wird auch das Ergebnis eines anderen Vergleichs mit der K 48 bestätigt, bei dem Baumwollgarn Ne 40 mit 19 500 U/min versponnen wurde.
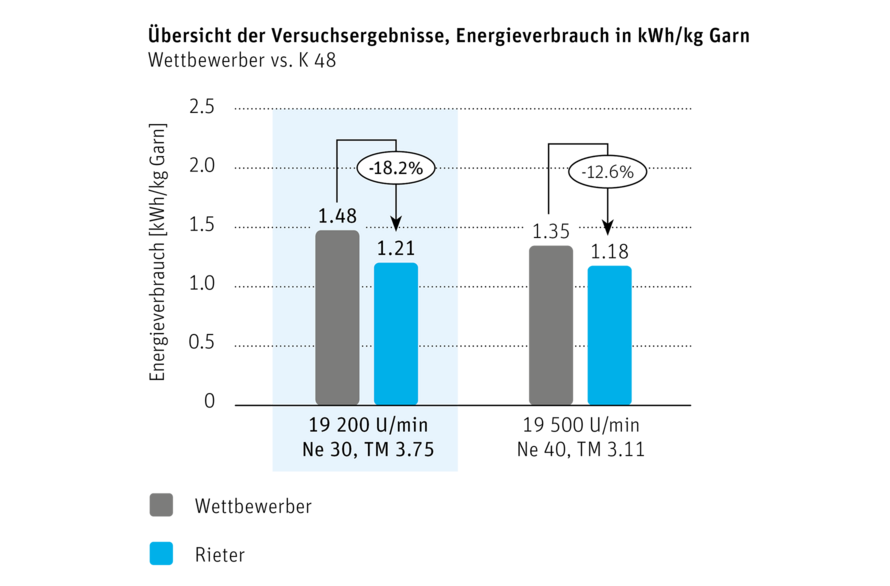
Gründe für diesen grossen Vorteil
Die grössten Energieverbraucher sind der Spindelantrieb (75–80%) und das Absaugsystem (12–17%). Ein Grossteil des übrigen Energieverbrauchs entfällt auf weitere Antriebe. (7–10%). In erster Linie ist das effiziente Absaugsystem für die grosse Energieeinsparung der Rieter-Kompaktspinnmaschinen verantwortlich. Die Wettbewerbermaschinen benötigen für die Kompaktierung jeweils ein zusätzliches Absaugsystem, was einen beträchtlichen zusätzlichen Energieverbrauch bedeutet. Die LENA-Spindeln sind ebenfalls ein wichtiger Faktor für den niedrigeren Energieverbrauch. Ihre Konstruktion und ihr Nutzeffekt wirken sich direkt auf die kWh pro kg Garn aus – verglichen mit Standard-Spindeln ist eine Energieeinsparung von 6% möglich.
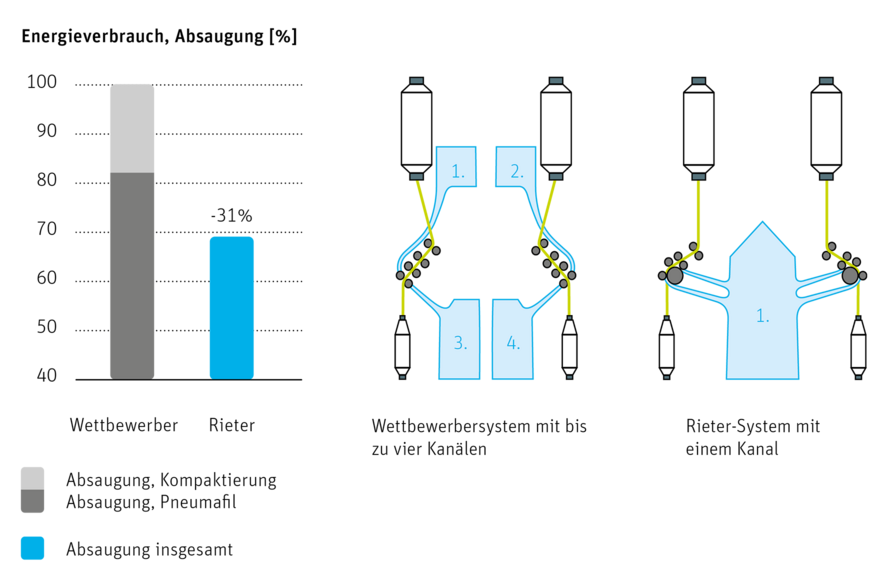
Zu guter Letzt erweist sich neben dem Absaugsystem und der Spindeldynamik auch der Nutzeffekt des Hauptmotorantriebs als wichtiger Faktor für den Energieverbrauch. Unser Engagement für eine optimale Energienutzung wird dadurch untermauert, dass wir hocheffiziente Hauptmotoren mit bis zu 110 kW Leistung und IE4-Technologie einsetzen.
Niedrigere Energiekosten sind greifbare wirtschaftliche Vorteile
Für Kunden ist es interessanter, dass sich diese Zahlen in greifbaren wirtschaftlichen Vorteilen niederschlagen. Bei einer Maschine mit 1 824 Spindeln entspricht die Reduzierung des Energieverbrauchs um 18% einer jährlichen Ersparnis von rund 12 000 USD pro Maschine (basierend auf Energiekosten von 0.1 USD pro kWh). Die geringeren Energiekosten machen unsere Maschinen zu einer strategischen Investition mit greifbarer Rendite und positionieren Rieter als Marktführer bei der nachhaltigen Produktion von Kompaktgarnen.