Rieter bietet die Systemlösung, mit der luftgesponnene Garne höchster Qualität aus 100% Baumwolle wirtschaftlich erzeugt werden können. Aus luftgesponnenen Garnen lassen sich Produkte mit sehr hochwertigem Charakter herstellen. Sie überzeugen mit angenehm weicher Haptik, einer gleichmässigen Oberfläche, einer hohen Pilling-, Wasch- und Formbeständigkeit sowie intensiven Farben.
Luftspinnsystem
Effizientes Luftspinnsystem für gekämmte Baumwollgarne- Höchste Rohmaterialausnutzung
- Signifikante Energieeinsparung
- Einmaliger weicher Griff im Gestrick
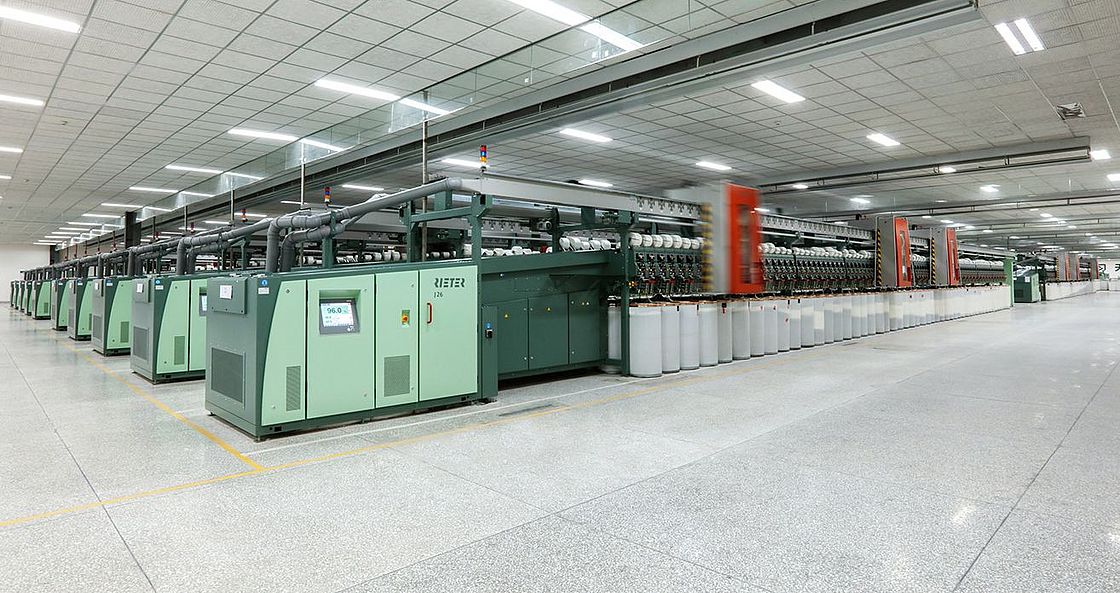
Stoffe mit hochwertigem Charakter
Die Stoffe aus dem Garn der Luftspinnmaschine J 26 haben eine einmalige Farbbrillanz. Die Oberfläche ist sehr gleichmässig, was vor allem auf der tiefen Haarigkeit basiert. Das ist die beste Voraussetzung für das Bedrucken von Stoffen. Die Konturen sind extrem scharf und klar. Endprodukte wie T-Shirts, Pullover und auch Handtücher haben einen sehr hochwertigen Charakter. Die Produkte überzeugen darüber hinaus in der täglichen Anwendung: Hohe Pilling- und Waschbeständigkeit, Formstabilität und intensive Farben – auch nach vielem Waschen – machen das Produkt langlebig und damit nachhaltig.
Luftspinnsystem für gekämmte Baumwollgarne
Exemplarisch wird ein Luftspinnsystem aufgezeigt, das aus einer Mittelstapelbaumwolle ein gekämmtes Garn der Feinheit Ne 30 produziert. Für einen Vergleich wurde die Rieter-Anlage einer «gemischte Spinnereianlage» gegenübergestellt, die aus Maschinen verschiedener Hersteller besteht. Die einzigartigen Garneigenschaften, wie die extrem geringe Haarigkeit, können zu einem höheren Garnpreis führen. Das Fallbeispiel geht trotz dieses Rieter-Vorteils von identischen Rohmaterial- und Garnpreisen für beide Systeme aus.

Zusätzlicher Cashflow mit dem Rieter-System: rund 1,8 Mio USD pro Jahr
- Rohmaterialausnutzung
+4%
- Energieverbrauch
-16%
- Platzbedarf
-25%
- Personalbedarf
-14%
Die Rieterlösung
Berechnungsgrundlage
Garnproduktion: 1 345 kg/h
Rohmaterialkosten: 2,00 USD/kg
Energiekosten: 0,074 USD/kWh
Rohmaterialausnutzung
Dank der erstklassigen Faservorbereitung, der effizienten Auskämmung an der Kämmmaschine E 90 und der optimalen Faserführung in der Spinneinheit der Luftspinnmaschine J 26 ist die Rohmaterialausnutzung des Rieter-Systems im Vergleich zum «gemischten System» um 4% besser. Ein beachtlicher Wert, bildet das Rohmaterial doch den grössten Kostenblock bei der Garnherstellung.
Energieverbrauch
Den grössten Beitrag bei der Energieeinsparung leisten die energiesparenden Einzelantriebe an den Spinn- und Spuleinheiten und die permanente Überwachung des Energieverbrauchs zur Erzeugung des Unterdrucks der Luftspinnmaschine J 26. Energieeffiziente Antriebskonzepte und innovative Maschinenkomponenten der Putzereilinie VARIOline und der Spinnereivorbereitungsmaschinen Karde, Strecke und Kämmmaschine leisten ebenfalls einen Beitrag zu niedrigen Energiekosten pro Kilogramm produziertem Faserband. Über das gesamte System können bis zu 16% Energie eingespart werden.
Platzbedarf
Mit den leistungsstarken Karden und Kämmmaschinen, den kompakten Strecken, dem beidseitigen Maschinenkonzept bei der J 26 und der hohen Maschinenleistung benötigt ein Rieter-System signifikant weniger Maschinen und damit 25% weniger Platz als andere Systeme. Effektiv können in diesem Beispiel sieben Karden, sechs Strecken, zwei Kämmereivorbereitungsmaschinen, sechs Kämmmaschinen und 25% Luftspinnpositionen eingespart werden. Das entspricht einem Platzbedarf von 3 500 m2.
Personalbedarf
Die Rieter-Anlage benötigt für die gleiche Produktion weniger Maschinen als die «gemischte Spinnereianlage». Das ermöglicht Personaleinsparungen von rund 14%.
Höherer Cashflow
Rohmaterialabgänge, Energie- und Arbeitskosten, den Verkauf von Garn und Kämmling, Zinsen und laufende Betriebskosten berücksichtigend, sind in der Gesamtrechnung die Produktionskosten der Rieter-Anlage für den gekämmten Luftspinnprozess niedriger als bei einem «gemischten System». Das bedeutet, dass Kunden, die auf das Rieter-Luftspinnsystem wie in unserem Beispiel setzen, bei gleicher Produktionsmenge einen um 1,8 Mio USD höheren Cashflow pro Jahr generieren als Kunden, die sich für eine «gemischte Spinnereianlage» entscheiden.
Einmalige Vorteile in der Weiterverarbeitung
Die J 26 kann – je nach Bedarf – Garne mit Z- oder S-Drehung produzieren. Das bringt Vorteile in der Strickerei. Durch das abwechselnde Zuführen von Z- und S-gedrehten Garnen wird die gestrickte Fläche formstabil, und der Griff wird sehr weich. Auch nach mehreren Waschgängen neigt die Ware nicht zum Verdrehen.
In der Weberei überzeugen die luftgesponnenen Garne mit einer sehr guten Schlichteaufnahme, was die Schlichtemenge und damit die Kosten reduziert. Nach dem Weben wird der Stoff gewaschen, wobei das Reinigen des Abwassers weniger aufwendig und damit umweltschonender ist. Die geringe Haarigkeit der J 26-Garne reduziert auch den Faserflug während des Webens. Das vermindert Ablagerungen auf der Webmaschine, die seltener gereinigt werden muss, was die Maschinenlaufzeiten erhöht.
Der System-Partner
Ein komplettes Rieter-System baut auf dem Know-how von Rieter im gesamten Spinnprozess auf: vom Rohmaterial bis zum Garn. Rieter offeriert alle vier am Markt etablierten Endspinnverfahren und bietet eine kompetente Beratung hinsichtlich der optimalen Spinntechnologie. Zudem unterstützen die Rieter-Experten beim Garnmarketing und bieten ein breites Spektrum an Serviceleistungen. Mit ESSENTIAL – der Rieter Digital Spinning Suite – wird die gesamte Spinnerei vernetzt und von einer Plattform aus gesteuert. Das gewährleistet hohe Qualität und optimale Effizienz, heute und in der Zukunft.