Energieefizienz
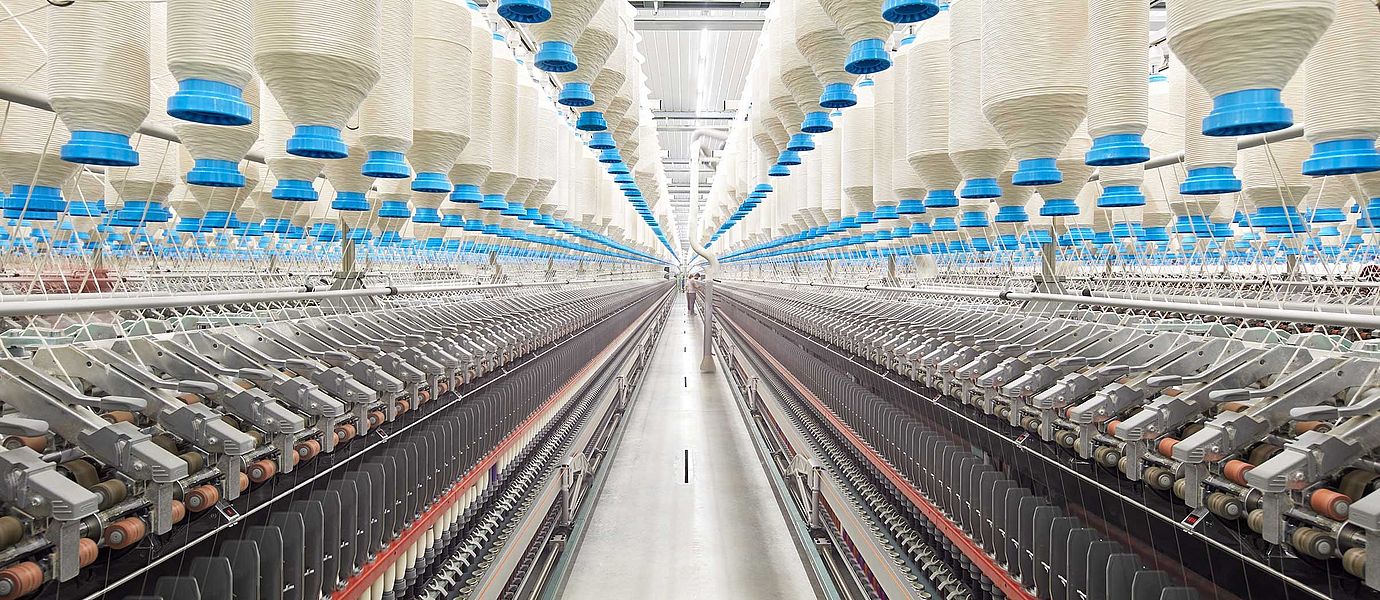
Energieeffizienz ist ein Markenzeichen von Rieter-Spinnsystemen. Klimawandel und steigende Energiekosten erfordern entschlossenes Handeln. Rieter setzt für 2030 messbare Ziele.
Energieeffizienz im Fokus
Rieter-Ingenieure legen bei der Entwicklung neuer Maschinen schon seit Jahrzehnten grossen Wert auf geringen Energieverbrauch. Das betrifft alle für den Spinnprozess relevanten Maschinen.
Das grösste Potenzial für Energieeinsparungen liegt jedoch im Endspinnprozess: Die Spinnmaschinen verbrauchen rund 60% bis 80% der für die Garnherstellung notwendigen Energie. Je feiner das Garn, desto höher die Motordrehzahl und damit der Energieverbrauch. Das trifft vor allem auf die Ringspinnmaschinen und Kompaktspinnmaschinen zu, die für feinere Garne zum Einsatz kommen. Die Luftspinnmaschinen benötigen elektrische sowie Druckluftenergie.
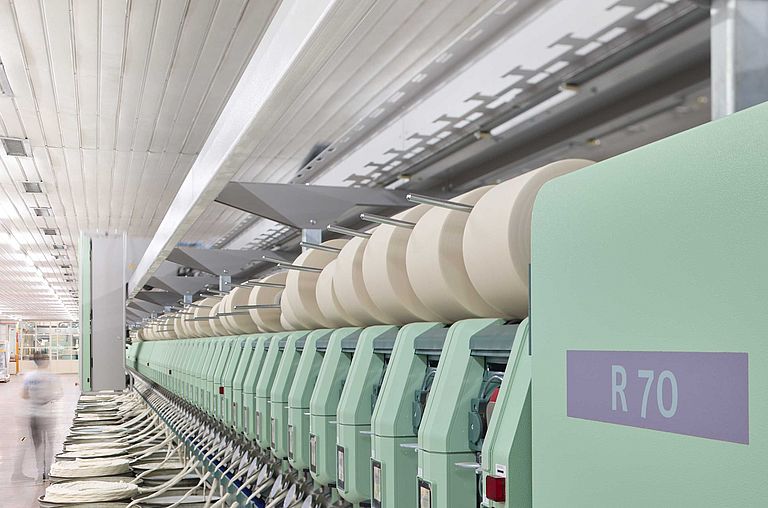
Die Rotorspinnmaschinen stehen im Vergleich zu den anderen drei Spinntechnologien für den geringsten Energiebedarf pro Kilogramm Garn. Seit dem Jahr 2000 hat Rieter den Energieverbrauch für die Produktion von 100 kg Viskosegarn der Feinheit Ne 30 im Vergleich zu heute deutlich gesenkt: um 37% beim Ringspinnsystem und um 54% beim Rotorspinnsystem. Beim Luftspinnverfahren gelang es Rieter seit 2008, den Energieverbrauch um 69% zu senken.
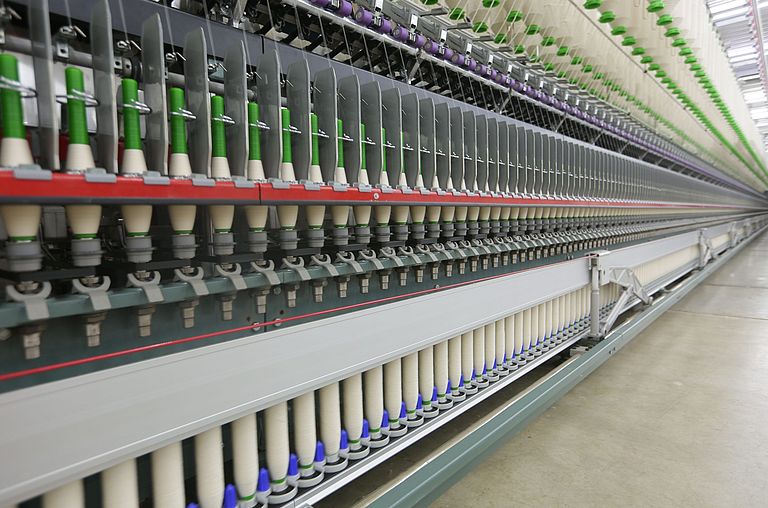
2025, 2030: Ambitionierte Weiterentwicklungen
Der Verbrauch der Ring- und Luftspinnsysteme soll im Vergleich zu 2021 bis 2025 um weitere 15% bzw. 16% und bis 2030 um 22% reduziert werden. Das soll insbesondere durch energiesparende Technologien und Weiterentwicklungen aller im Prozess vorhandenen Maschinen erfolgen. Auch die neue Luftspinnmaschine J 70 spielt hier eine wichtige Rolle. Der Energieverbrauch des vergleichsweise hocheffizienten Rotorspinnsystems soll bis 2025 um 2% und bis 2030 um weitere 5% gesenkt werden.
Die zwei nachstehenden Beispiele stehen exemplarisch für die Bemühungen von Rieter, Maschinen und Systeme insbesondere im Hinblick auf den Energieverbrauch zu optimieren.
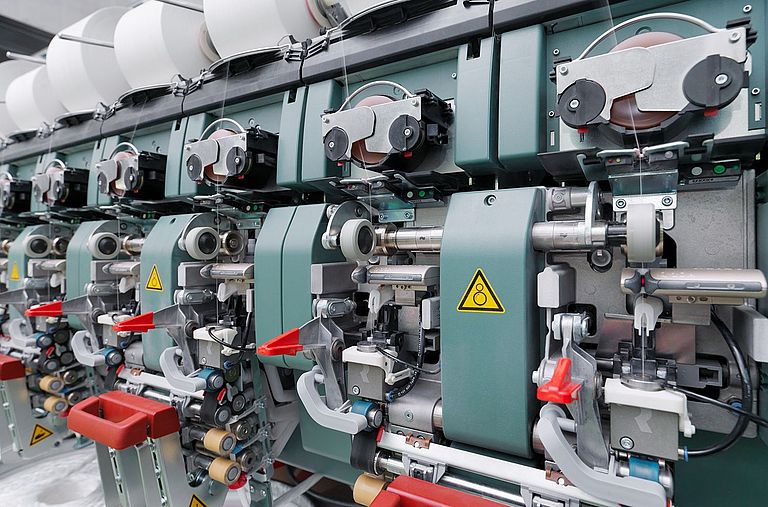
Luftspinnmaschine J 26 – gezielte Innovation für mehr Effizienz
Das Luftspinnen ist eine noch relativ junge Technologie. Ihre hohe Produktivität und die einzigartigen Eigenschaften der Garne werden zu ihrem starken Wachstum in den nächsten Jahren beitragen. Neben der elektrischen Energie für die Antriebe und das Absaugsystem benötigt die Luftspinnmaschine Druckluft für die Drehungserteilung während der Garnbildung.
Die Integration eines effizienten Absaugsystems und energiesparender Antriebe in die neueste Luftspinnmaschine J 70 führte zu einer 3%igen Reduktion des Stromverbrauchs pro Kilogramm Garn im Vergleich zum Vorgängermodell. Darüber hinaus weist die J 70 einen um 5% geringeren Druckluftverbrauch pro Kilogramm Garn auf. Erreicht wird dies durch höhere Liefergeschwindigkeiten bei gleichem Druckluftverbrauch und geringerem Eingangsdruck. Dass die J 70 auch bei Klimaschwankungen robust läuft, wird in feuchten und heissen Regionen sehr geschätzt. Die Aufrechterhaltung eines optimalen Spinnklimas in der Spinnerei verbraucht enorm viel Energie.

Rundum effizient
Die Karde ist ein fester Bestandteil in jedem Spinnsystem. Sie löst Faserflocken zu Einzelfasern auf und parallelisiert diese. Ihr Anteil am Energieverbrauch des Spinnprozesses beträgt bis zu 15%. Die aktuelle Karde C 81 ist zentral für die Erreichung der Effizienzziele bis 2025.
Sie benötigt halb so viel Energie wie das Kardenmodell C 51 aus dem Jahr 2000, und sie produziert 40% mehr Faserband als ihr direktes Vorgängermodell. Damit benötigt eine heutige Spinnerei bei gleicher Produktion weniger Karden. Das senkt den Energieverbrauch und damit auch die Produktionskosten.
Effizienzsteigerungen
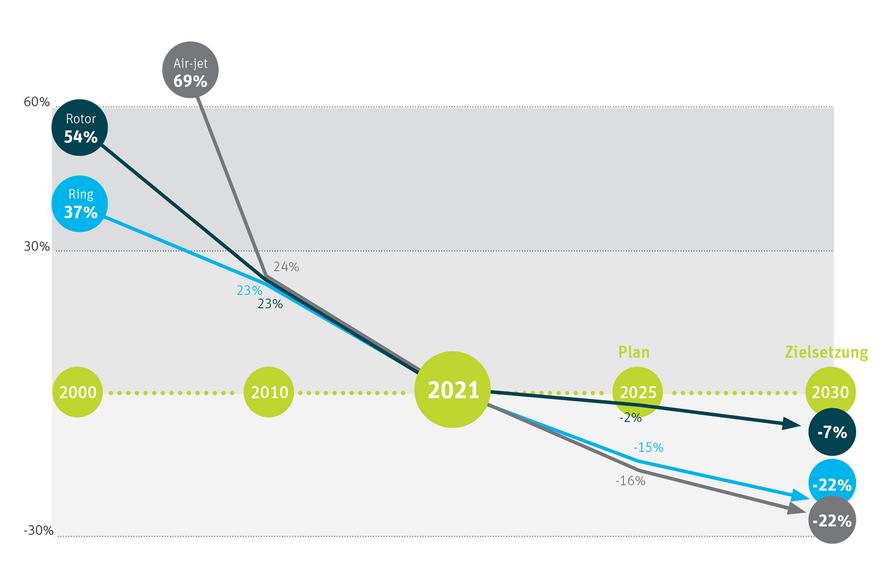
Energieeffizienz der Spinnsysteme
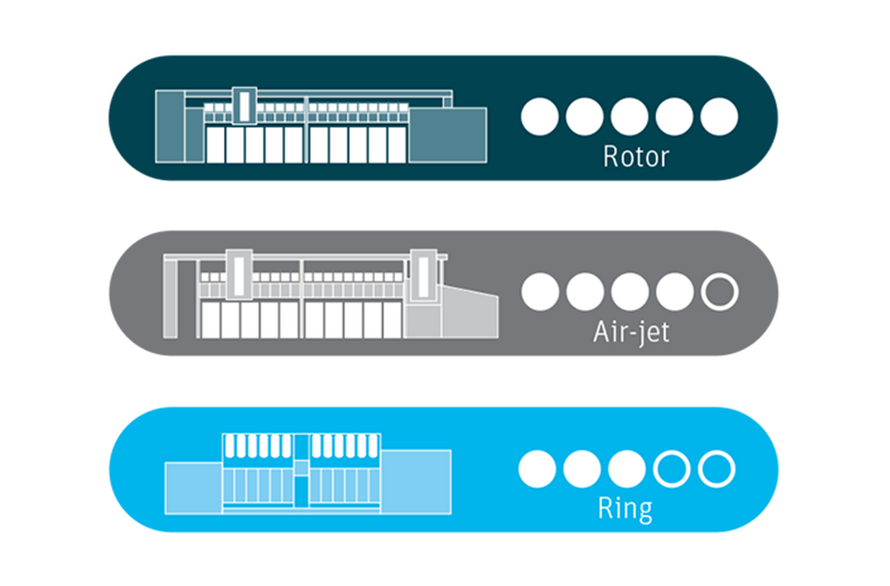
CO2 in der globalen Modeindustrie
Die Modeindustrie ist für rund 4% der weltweiten Treibhausgasemissionen verantwortlich. Ohne zusätzliche Reduktionsmassnahmen könnten diese bis ins Jahr 2030 um ein Drittel ansteigen, prognostiziert der Bericht «Fashion on Climate» (2020)1. Der Anteil der Garnherstellung an den Gesamtemissionen der Branche beträgt laut der Studie rund 8%. Damit verursacht die Garnproduktion 0.32% der globalen Treibhausgasemissionen. Verglichen mit anderen Sektoren ist diese Zahl zwar relativ klein, aber Rieter ist der festen Überzeugung, dass jeder Beitrag zur Senkung der Emissionen wichtig ist. In Zeiten steigender Energiekosten trägt Energieeffizienz darüber hinaus zur Wettbewerbsfähigkeit der Spinnereien bei.
1 McKinsey and Global Fashion Agenda. (2020). Fashion on Climate.