Rieter offers the system solution with which air-jet yarns of the highest quality can be produced economically from 100% cotton. Air-jet yarns enable products with a very high-quality character to be produced. They impress with their pleasantly soft touch, uniform surface, high resistance to pilling and washing, shape retention, and intense colors.
Air-Jet Spinning System
Efficient air-jet spinning system for combed cotton yarns- Maximum raw material utilization
- Significant energy saving
- Unique soft touch of knitted fabrics
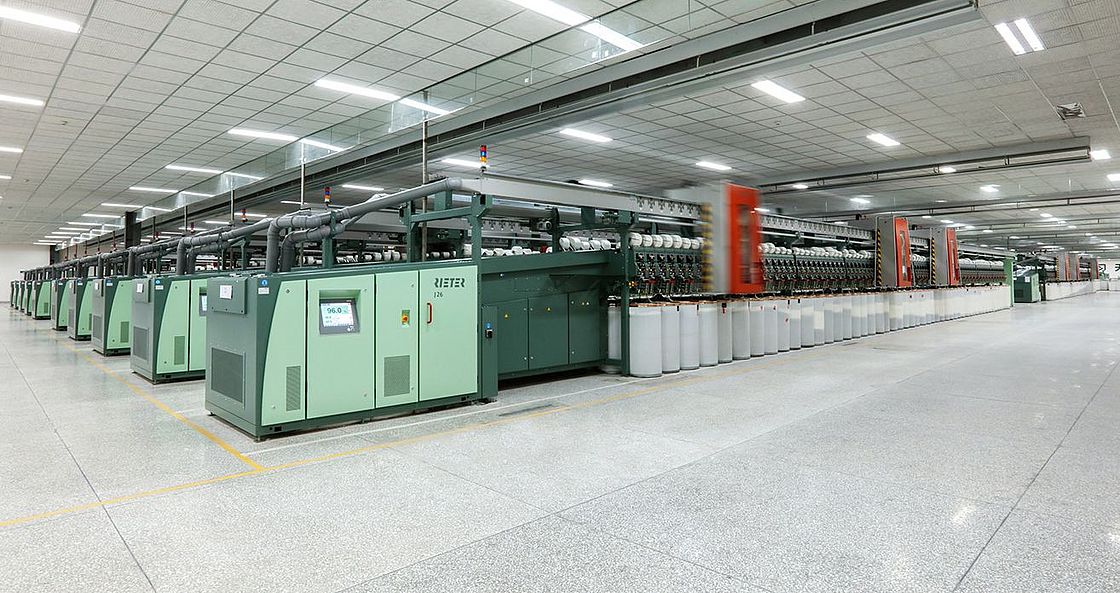
Fabrics with high-quality character
The fabrics produced from yarn spun on the air-jet spinning machine J 26 have a unique color luster. The surface is very uniform, which is primarily based on the low hairiness. This is the ideal prerequisite for printing on fabrics. The contours are extremely clear and defined. End products such as T-shirts, sweaters, and terry towels have a very high-quality character. The products also impress in daily use: High resistance to pilling and washing, maximum shape retention, and intense colors – even after many washes – ensure a long-lasting and therefore sustainable product.
Air-jet spinning system for combed cotton yarns
The example used here is of an air-jet spinning system that produces a combed yarn with a count of Ne 30 from a medium-staple cotton. To enable a comparison to be made, the Rieter system was contrasted with a “mixed spinning mill” consisting of machines from various manufacturers. The unique yarn characteristics, such as the extremely low hairiness, can increase the yarn price. However, the case study does not take this benefit of using Rieter machines into account, and is instead based on raw material prices and yarn prices for both systems being the same.

Additional cash flow with the Rieter system: around USD 1.8 million per year
- Raw material utilization
+4%
- Energy consumption
-16%
- Space requirement
-25%
- Personnel requirement
-14%
The Rieter Solution
Basis of calculation
Yarn production: 1 345 kg/h
Raw material costs: 2.00 USD/kg
Energy costs: 0.074 USD/kWh
Raw material utilization
Thanks to the top-quality fiber preparation with efficient noil extraction on the comber E 90, as well as the optimal fiber guiding in the spinning unit of the air-jet spinning machine J 26, the raw material utilization of the Rieter system is absolute 4% higher compared a “mixed system”. This value is impressive, as the raw material is the biggest cost factor in yarn production.
Energy consumption
The energy-saving individual drives on the spinning and winding units and the permanent monitoring of energy consumption for vacuuming on the J 26 make the largest contribution to saving. Energy-efficient drive concepts and innovative machine components in the blowroom line VARIOline and the spinning preparation machines (i.e. the card, draw frame and comber) also play a part in keeping the energy costs per kilogram of sliver produced low. Energy savings of up to 16% can be made across the entire system.
Space requirement
With the powerful cards and combers, the compact draw frames, the double-sided machine concept of the J 26 and the high machine performance, a Rieter system requires significantly fewer machines and consequently 25% less space than other systems. In this example, seven cards, six draw frames, two combing preparation machines, six combers and 25% air-jet spinning positions can effectively be saved. This is equivalent to a space requirement of 3 500 m2.
Personnel requirement
The Rieter system requires fewer machines than the “mixed spinning mill” for the same production output. This makes it possible to achieve personnel requirement savings of around 14%.
Additional cash flow
Taking raw material waste, energy and labor costs, sales of yarn and noil, interest rates and ongoing operating costs into consideration, the total production costs of the Rieter system for the combed air-jet spinning process are lower than those of a "mixed system". This means that, with the same production volume, customers who invest in the Rieter air-jet spinning system as per our example generate a cash flow that is around USD 1.8 million per year higher than that of customers who opt for a “mixed spinning mill”.
Unique Advantages for Downstream Processing
The J 26 can produce yarns with Z- or S-twist as required. This is beneficial in the knitting mill. By alternately feeding Z- and S-twisted yarns, the knitted surface becomes dimensionally stable and the touch becomes very soft. Even after several washing cycles, the products do not tend to be affected by spirality.
In weaving mills, the air-jet yarns convince with a very good size pick-up, which lowers the size amount and therefore reduces the costs. After weaving, the fabric is washed, whereby the cleaning of the waste water is less elaborate and thus more environmentally friendly. The low hairiness of the J 26 yarns also reduces the fiber fly during weaving. This minimizes deposits on the weaving machine, meaning it needs to be cleaned less often, which in turn increases machine running times.
The system partner
A complete Rieter system is established on Rieter’s expertise throughout the entire spinning process: from processing raw material to yarn. Rieter offers all four end spinning processes and provides professional advice on the optimal spinning technology. Furthermore, experts provide support with yarn marketing and offer a wide range of services. The entire spinning mill is networked and controlled from a single platform with ESSENTIAL – Rieter Digital Spinning Suite. This guarantees high quality and optimal efficiency, both now and in the future.