Smart and Efficient – ESSENTIALorder
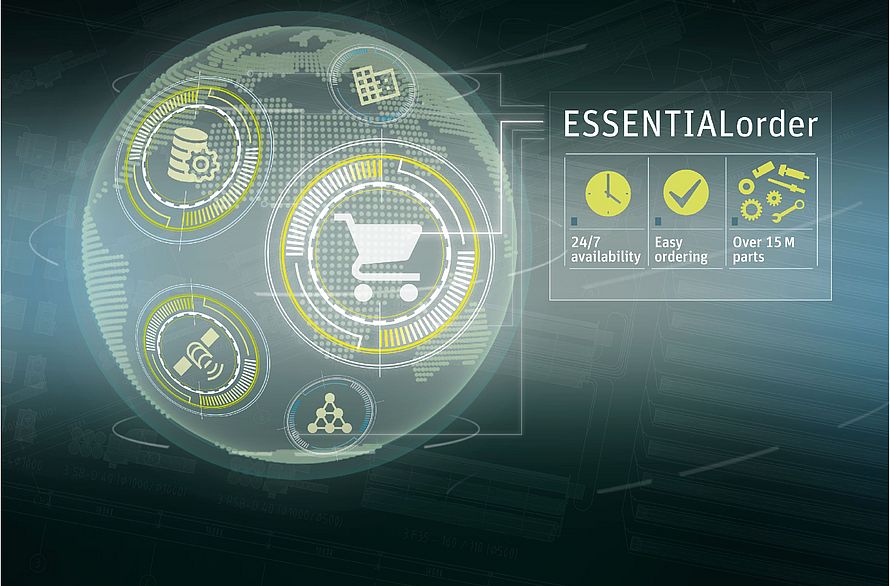
Fig. 1: ESSENTIALorder: The webshop for spare parts management
Order management is a challenging task for spinning mills, as machines are made of thousands of parts and supply chains are more complex than ever. In addition, it is important to manage stock levels efficiently. Vardhman Group’s 10 spinning mills count on Rieter’s webshop to order OEM spare parts around the clock in just a few clicks. ESSENTIALorder offers more than 14.5 million spare parts online. The platform simplifies ordering and enables optimization of stock levels.
Vardhman is India's largest vertically integrated textile manufacturer, with 10 spinning mills across the country. Vardhman's central purchasing team uses a monitoring system and bases its purchasing decisions on real-time data. Rieter machines are running in all 10 spinning mills and thus are distributed over various locations. The purchasing team set a goal of optimizing their process for procuring Rieter OEM spare parts. Vardhman therefore turned to Rieter for an online solution that simplifies ordering and checks the availability of spare parts in real time, with lead time included.
The One Stop Solution for Spares Ordering
Rieter's after sales team introduced the webshop ESSENTIALorder (Fig. 1) to two of Vardhman’s units in Northern India back in 2019. After the successful launch of the webshop in these two spinning mills, ESSENTIALorder was introduced to the remaining Group units. The simple, easy-to-use ordering process impressed the purchasing team. Today, all 10 of Vardhman's spinning mills have been using the ESSENTIALorder webshop for more than three years.
Simple and Efficient
ESSENTIALorder has more than 14.5 million spare parts online and is available 24 hours a day, seven days a week. The webshop accesses the machine configurations available in the system to provide a personalized shopping experience. It facilitates order management, enabling spinning mills to optimize their internal stock levels. ESSENTIALorder enables customers to check the price, availability, and lead time before ordering. Customers can download quotes, order confirmations, and invoices on demand. Order and shipping status are available for customers to check the real-time status of their orders. The built-in customized visual catalog (Fig. 2) enables the user to select the correct parts for the respective machine. Additional key benefits include the ability to:
- ensure compatibility of spare parts with equipment design,
- simplify recurring orders via the order history,
- assign roles allowing different functionalities to different users,
- choose who can access and create orders, set quantity limits and track orders, and
- easily order multiple spare parts by uploading a CSV file.
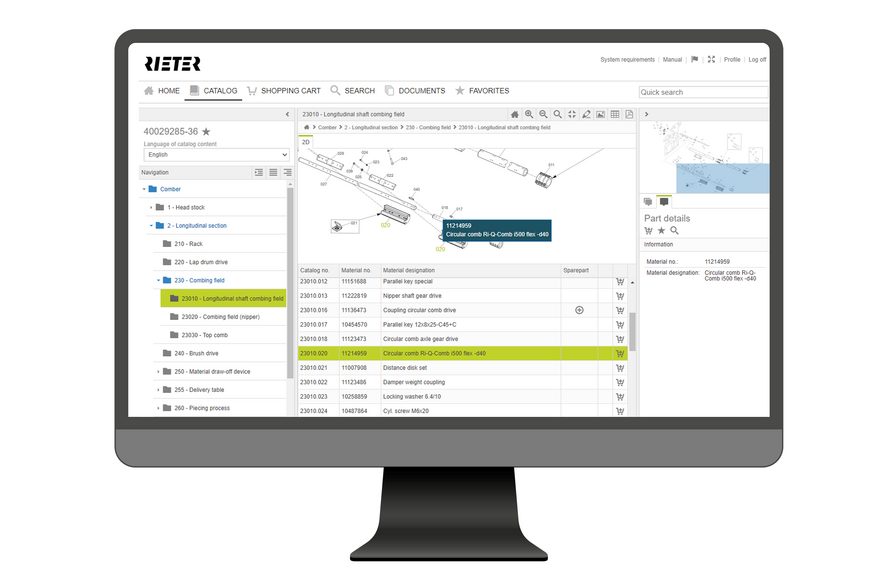
More and more spinning mills are ordering through the webshop. Vardhman has placed the most orders to date (Fig. 3). The spinning mill team headed by Neeraj Jain, Joint Managing Director, appreciated the efforts taken by Rieter:
“As a user of ESSENTIALorder, our order management process has become much easier and our different spinning mills are optimizing stock levels effectively. ESSENTIALorder is a user-friendly and reliable platform, as spare parts for Rieter spinning machines can be ordered around the clock in just a few clicks."Neeraj Jain, Joint Managing Director, Vardhman
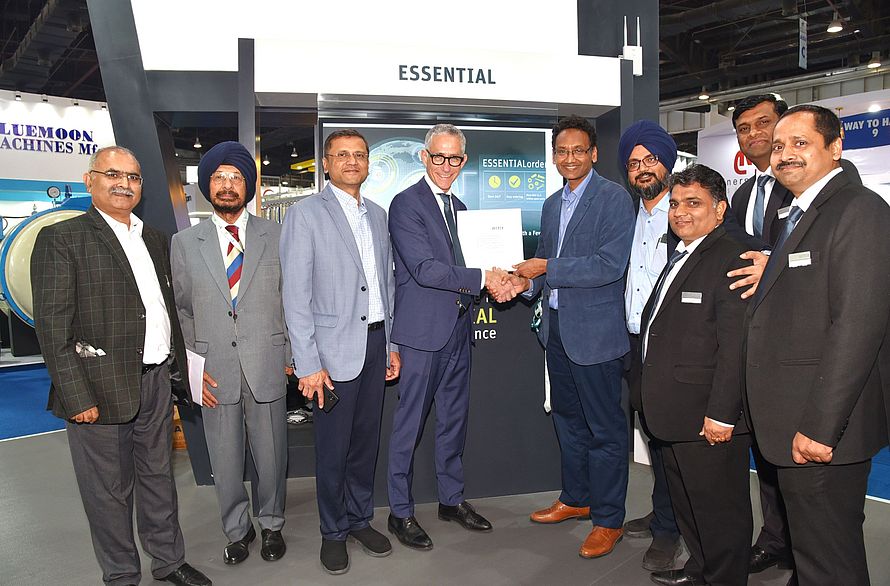