The strength of the Rieter rotor spinning system has always been its high productivity and achievement of a consistent yarn quality, particularly in applications with shorter fibers. The new rotor direct process further greatly enhances system performance and yarn quality – even with cost-effective raw materials.
Rotor Spinning System
Productive spinning with high short-fiber content- Low raw material costs
- High productivity
- Consistently high yarn quality
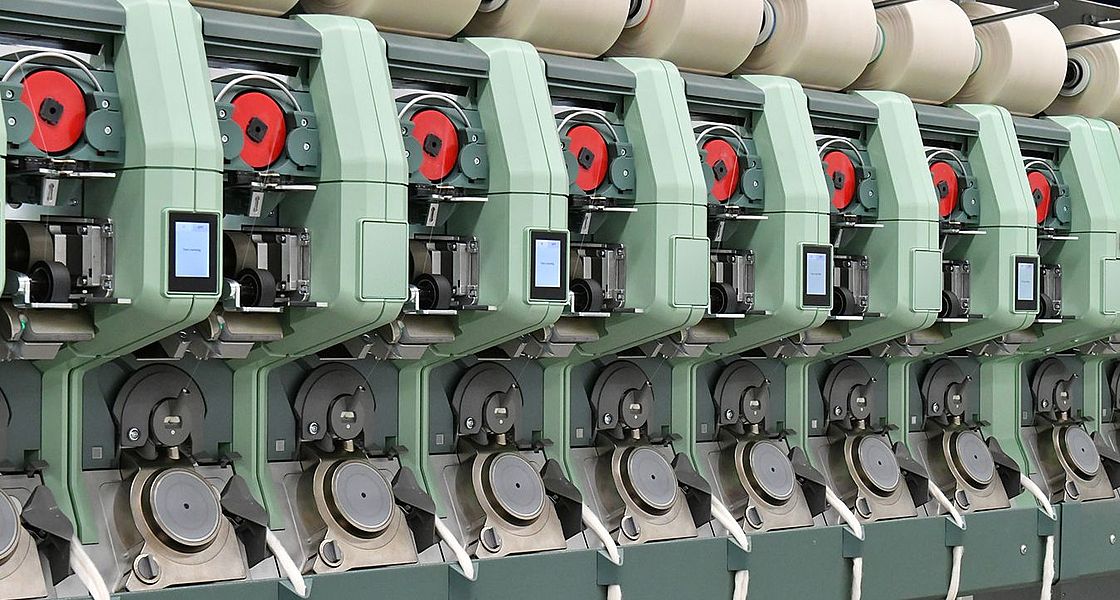
Rotor spinning system
The fully automatic rotor spinning machine R 70 sets new benchmarks in rotor yarn production. In addition to the proven Rieter spinning technology with low ends down and high productivity, it offers greater efficiency through individual piecing at each spinning position. Furthermore, the R 70 is capable of processing even raw material that has a high trash content into a yarn of an accordingly high quality. This enables spinning mills to reduce their raw material costs. In this example, the R 70 was combined with the high-performance card C 80 and the autoleveler draw frame module RSB-Module 50. A yarn with a count of Ne 21 was spun from this. A “mixed spinning mill”, which is equipped with machines from two different manufacturers, was used for comparison.

Additional cash flow for the Rieter system: around USD 330 000 per year
- Raw material costs
-2%
- Productivity
+5%
- Energy consumption
-7%
The Rieter Solution
Basis of calculation
Rotor boxes: 420
Productivity with Rieter system: +5%
Energy costs: 0.074 USD/kWh
Raw material costs
Using the optimum raw material is an important factor in minimizing production costs. The rotor spinning machine R 70 with the improved spinning box and optimized BYpass enables more cost-effective raw materials with a higher noil or trash content to be spun into a high-quality yarn. With the rotor direct process and the rotor spinning machine R 70, in this comparison the customer can replace a bale of virgin cotton with a bale of waste in the bale laydown and still achieve a comparable yarn quality. This means the raw material costs are reduced by 2% with the Rieter system.
Productivity
The key to the high productivity of the Rieter system is the optimized spinning box of the rotor spinning machine R 70. This achieves improved spinning stability and higher yarn tenacity. The higher tenacity can be translated directly into higher productivity by reducing the yarn twist.
Energy consumption
Energy-efficient drive concepts, innovative machine components, and the high production output of the C 80 with the RSB-Module 50 save energy. Further significant energy savings are achieved with the R 70 thanks to the optimized individual drives, extremely efficient suction, energy-saving automatic filter cleaning, and optimized air routing. The complete Rieter rotor spinning system saves up to 7% energy compared to a «mixed spinning mill».
Yarn quality
In terms of yarn evenness, the card C 80 combined with the RSB-Module 50 with two draft zones offers significant advantages over a draw frame module with only one draft zone. Compared to other rotor spinning machines, the combination of modern spinning and piecing technology in the R 70 leads to far superior tenacity and yarn evenness. This means, for example, that a yarn with high evenness can be produced from a cotton blend that has a noil content of over 50% – even with yarns that have a finer count than Ne 30 and at maximum productivity.
Additional cash flow
The R 70 enables spinning with a high trash content, and therefore the use of more cost-effective raw materials. In the example, the same attainable yarn price was used for both the Rieter system and the “mixed system”. Taking energy and labor costs, interest rates and ongoing operating costs into consideration, the total production costs of the Rieter system for the short rotor spinning process are significantly lower than those of a solution from a mix of suppliers. This means that customers who invest in the Rieter rotor spinning system as per our example generate a cash flow that is around USD 330 000 per year higher than that of customers who opt for a “mixed spinning mill”.
The system partner
A complete Rieter system is established on Rieter’s expertise throughout the entire spinning process: from processing raw material to yarn. Rieter offers all four end spinning processes and provides professional advice on the optimal spinning technology. Furthermore, experts provide support with yarn marketing and offer a wide range of services. The entire spinning mill is networked and controlled from a single platform with ESSENTIAL – Rieter Digital Spinning Suite. This guarantees high quality and optimal efficiency, both now and in the future.