Suction Drum Refurbishment Improves Yarn Quality
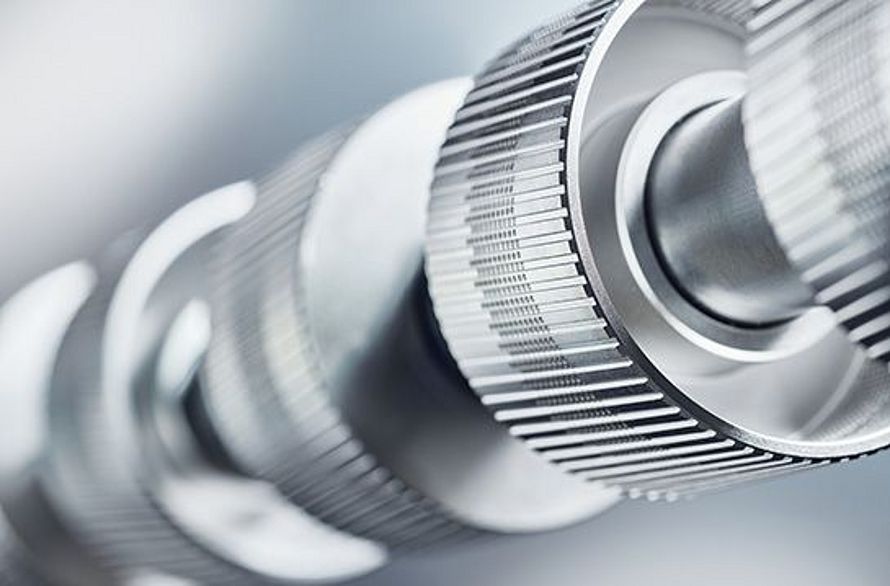
Improved wear-resistant coated suction drum mounted on the bottom roller shaft after refurbishment by Rieter repair services.
After several years of continuously operating compact suction drums, they may show signs of surface wear. The refurbishment of the suction drums by Rieter’s repair service is a cost-efficient, proven solution that helps restore original yarn quality. Several customers experienced a reduction in yarn imperfections by up to 23% and a reduction in the hairiness index by up to 13% after refurbishment while processing cotton on their Rieter compact-spinning machines.
The aging of machine components is inevitable, especially in the high-intensity environments of spinning mills. In the case of Rieter compact-spinning machines, the suction drum is a decisive technological component and significantly contributes to producing a high-quality compact yarn. After several years in operation, some suction drums may exhibit signs of wear and tear. Various parameters can impact the lifetime of the drums. They include hours of machine operation, maintenance practices, handling of the drums during operation, type of fibers processed and site ambient conditions, including temperature, humidity and dust. These parameters can also affect the performance of the complete compact-spinning machine and may result in compact yarn with inferior quality.
Reliable, long-lasting and cost-efficient solution
The suction drums are assembled in a group of eight pieces fixed to a single bottom roller shaft. Even in cases of single drum damage, various service providers tend to replace the whole drum assembly. This practice is neither economical nor sustainable. Equipped with the know-how of the Original Equipment Manufacturer, Rieter repair services can refurbish the drums that show significant wear and tear, providing a reliable, long-lasting and cost-effective repair solution.
The repair is carried out by trained Rieter technicians who are equipped with a special state-of-the-art suction drum refurbishment machine. During the repair process, the eccentricity values of all the suction drums and the bottom roller shafts are thoroughly inspected, ensuring they are well within Rieter standards.
Improved yarn quality and productivity with suction drum refurbishment
The below graph shows the improvement in yarn quality after the suction drum refurbishment:
- imperfections reduced by up to 23%,
- hairiness index reduced by up to 13% and
- unevenness value reduced by up to 7%.
Quality consistency between spindles is ensured and the periodic faults due to wear and tear of suction drums are eliminated, resulting in a better and more uniform fabric appearance. The spindle speed was increased as there was consistent yarn quality and better running performance with reduced yarn breakages, resulting in higher yarn production.
The suction drum refurbishment service provided by the Rieter service center in Kahramanmaraş, Türkiye, helped us overcome quality and performance problems due to drum deterioration. It also helped increase the productivity of our machine. Drum replacement restored compacting effectiveness, working performance of the machine and quality levels of yarn. Thus, an improvement in overall quality was achieved. The Rieter service team also conducted a complete overhaul during the refurbishment and a complete review of the standards was conducted to ensure all quality standards were met.Tülay Fidan, Quality Manager of Almer Tekstil, Türkiye
The suction drum refurbishment at Rieter’s Kahramanmaraş repair service center helped us restore the original performance of the compact-spinning machine. The quality of the refurbishment process was so impressive and we are very happy with the performance of the machine.Halil Çetin, General Manager of MEM Tekstil, Türkiye
The refurbishment resulted in the following improvements:
- 40% reduction in yarn breaks,
- 10% increase in production due to a higher spindle speed of 1 500 rpm,
- reduction in yarn hairiness value and hairiness variation from spindle to spindle,
- reduction in imperfections and periodic faults and
- fewer yarn cuts in winding resulting in reduced hard waste.