Single-Head Draw Frames: Breakthrough in Flexibility at Dezhou Huayuan
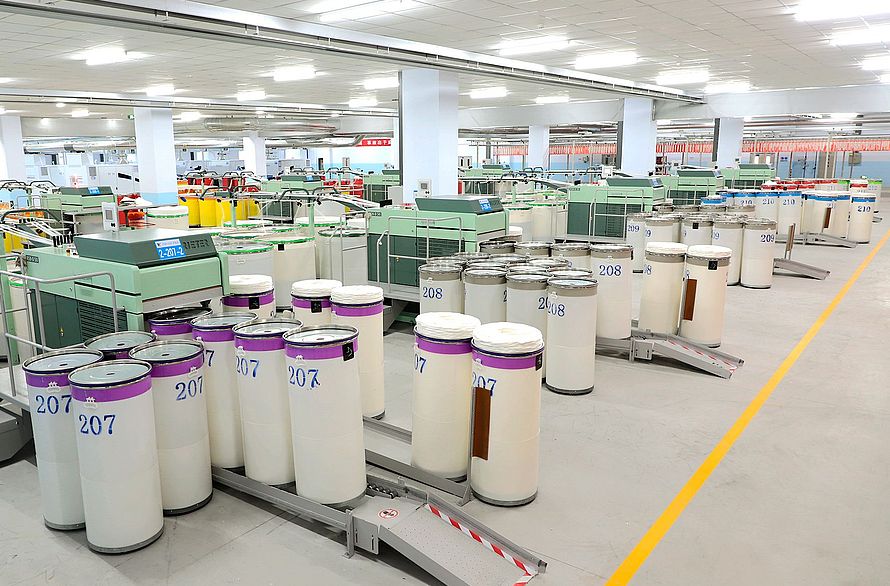
In response to the ongoing shortage of labor and in anticipation of stringent high-quality yarn demands, Dezhou Huayuan Eco-Technology Co., Ltd. took action in 2022. The company decided to phase out all outdated draw frames. Subsequently, they acquired a total of 126 units of Rieter’s single-head draw frames, namely the autoleveler draw frame RSB-D 50 and the draw frame without autoleveling SB-D 50. This step underscores the company’s commitment to staying at the forefront of technology, enhanced their quality and led to notable savings in conversion costs.
The Challenge
The shortage of operators is one of the major challenges faced by Dezhou Huayuan, which also happens to be one of the most significant issues in the textile industry at present. During the processing of special fibers like modal, recycled viscose and polyester, blends of wool and silk with acryl, etc. the workload on operators is even greater compared to spinning standard fibers. This is caused by faster variations in order intake and the heightened sensitivity of machine behavior to climate changes when processing special fibers.
Maintaining consistently high yarn quality despite the shortage of skilled staff is the second challenge Dezhou Huayuan is concerned about. With multiple draw frame lines, the technological settings must be changed daily. Hence, there is a pressing need to decrease the time required for preparing the technology for each order, optimize the utilization of each draw frame line, and thereby expand the annual order output.
Enhancing raw material utilization is the third challenge of Dezhou Huayuan, as special fibers have a high price and purchasing volume is limited. In-mill experiences show that raw material costs account for over 60% of the total yarn conversion costs. Consequently, every kilogram of waste directly reduces the profitability of the spinning mill.
The Solution
The innovative Rieter draw frames (R)SB-D 50 bring a remarkable enhancement in productivity through precise fiber drafting and blending, while also ensuring reduced maintenance requirements due to its robust design. Rieter’s draw frames empower textile manufacturers with the ability to quickly change between diverse production orders, thanks to its user-friendly interface which enables rapid adjustments. Furthermore, its operation requires fewer operators, resulting in optimized labor utilization. The integration of the expert system SLIVERprofessional includes recommended settings for different raw material and other parameters. With its advanced coiler sensor technology, the draw frames limit material wastage and enhance sustainability in production processes. By combining these advantages, Rieter draw frames represent a significant advance in modern textile manufacturing that increases quality, efficiency and sustainability.
In the draw frame process, waste of raw material is an essential challenge. This waste is primarily attributed to suboptimal coiling of the initial layers within the can (Fig. 1), resulting in compromised quality and sliver breaks during following processing stages. To maintain stringent quality standards for custom-made orders and prevent mixing with other orders, operators are forced to remove these imperfect layers by hand.
The root cause of this issue is typically a low-hanging can plate (Fig. 2), a common and unavoidable occurrence in mills due to poor can quality and aging can springs.
To address this problem, Rieter has developed an innovative solution involving a light barrier system. This system switches the can-filling process to high speed only when the sliver is consistently in contact with the coiler (Fig. 3). This innovation ensures the proper coiling of sliver, even in the initial layers, and ultimately saves valuable raw material.
The Customer’s Benefits
At Dezhou Huayuan, the single head draw frames RSB-D 50 achieved an impressive field running speed of 700 m/min in special fiber spinning, equivalent to the output of two competitor draw frame heads. This allows the maintenance of multiple production lines capable of handling diverse orders and resulting in substantial conversion cost savings.
For a 3.5 ton special spinning order, for example, the RSB-D 50 production line completes the job within 24 hours and fits seamlessly into the order change plan for the next day. This not only reduces operator working hours by 1.4 per day but also enables an annual order volume increase of 6%.
In addition, the expert system SLIVERprofessional rationalizes the technology setup and enables more than 60% faster job adjustments compared to competition at Dezhou Huayuan. It provides process recommendations and user-friendly controls for suction intensity and reel speed. The integration of the RSB-D 50 reduces the need for technicians from 3 to 1, saving significant time in the daily setup of multiple production lines.
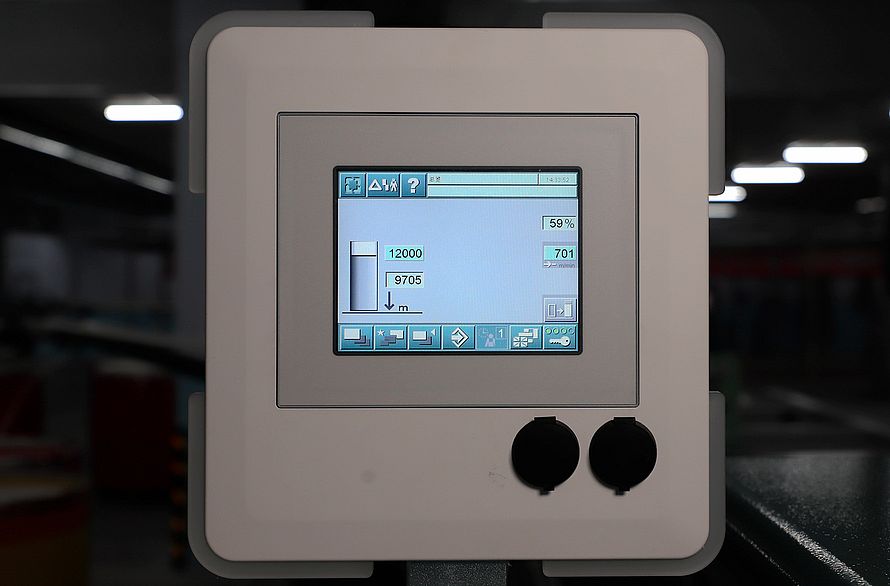
The Customer’s Benefits with the SB-D 50
Dezhou Huayuan is the first customer in China to invest in Rieter’s state-of-the-art SB-D 50 single-head draw frame. This strategic investment represents a significant milestone for Dezhou as it takes the company to a higher level in terms of operational flexibility, personnel optimization and significant waste and energy consumption reduction.
In a comparative analysis with competitor solutions, the investment in the SB-D 50 brings a number of significant benefits as shown below (calculated for 10 machines).
Dezhou Huayuan’s investment not only enhances efficiency but also boosts profitability, making it a strategic choice in the spinning industry.
The Rieter draw frames (R)SB-D 50 consistently deliver top-notch performance, ensuring the highest quality while significantly reducing the cost for operators, raw material, and energy. By investing in Rieter draw frames SB-D 50, we have realized annual savings of approximately CNY 600 000 calculated per 10 machines compared to competitor solutions. This outstanding cost-effectiveness positions us competitively in the years following the draw frame investment, with a remarkable payback period of just 2 years.Niu Jianwei, Vice general manager of Dezhou Huayuan Eco-Technology Co., Ltd.
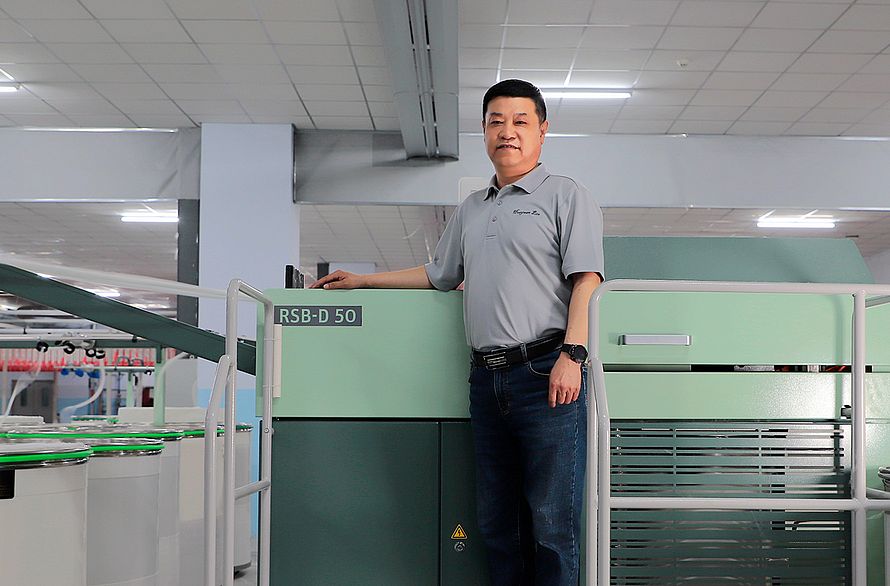
Download
About Dezhou Huayuan
Dezhou Huayuan Eco-Technology Co., Ltd. is a modern high-tech enterprise specializing in production of new differentiated fiber yarns. The company was established in July 2002 and is located in Tianqu Industrial Park, Decheng District, Dezhou City. It has three production subsidiaries, producing differentiated yarn from regenerated cellulose fiber, superfine blended acrylic fiber, lyocell, wool, linen, cashmere and other multi-components.
Dezhou Huayuan Eco-Technology Co., Ltd.
1100 Geruide Road
253000 Dezhou
China