Suction Tube: A Small Part with a Big Impact
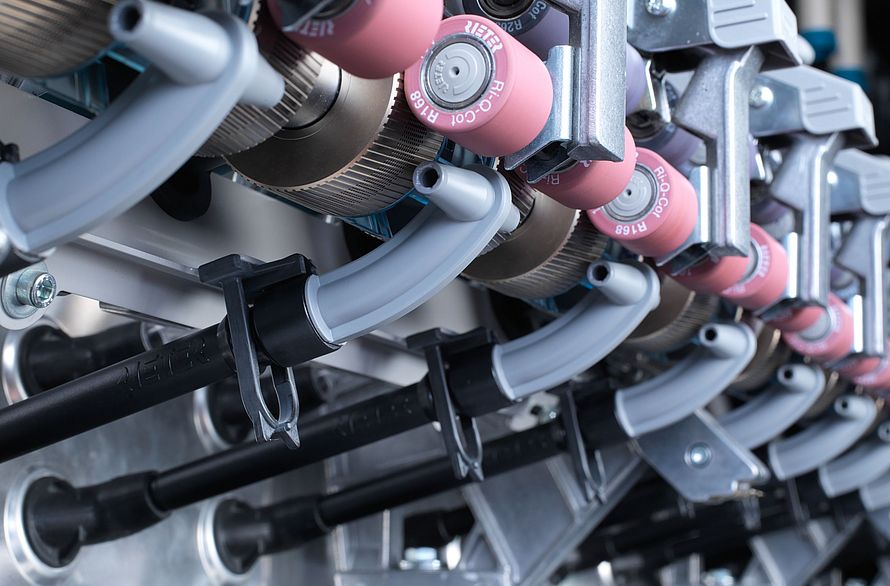
The optimized suction tube ECOrized can reduce the energy requirements of compact-spinning machines.
Reducing energy consumption is valuable, especially in end spinning, where energy requirements are particularly high. The optimized suction tube ECOrized for compact-spinning machines has proven itself millions of times over in new machinery and is an attractive retrofit for older models. An Indian customer with 14 retrofitted compact-spinning machines is saving around CHF 36 000 each year. And the yarn quality has remained consistently high.
The demands that spinning mills place on their textile machines are as varied as the products they produce. Yet mill owners all agree on one point: The energy consumption of their machines should be as low as possible. The energy consumption costs form a large part of the yarn conversion costs, which means they play a key role in a spinning mill’s profitability.
For many decades now, Rieter has been focusing on low energy consumption during machine development. Once new products have been successfully launched on the market, their suitability for retrofitting is tested and, if possible, they are offered as an upgrade for existing machine generations. It is no secret that end spinning machines in particular consume a very large proportion of the energy used in yarn conversion. Every optimization in this area is valuable, which becomes very clear in the conversion costs per kilogram of yarn. This means that upgrading end spinning machines to reduce their energy requirements quickly pays off and makes spinning mills more economical.
Profitable Investment
An important Indian customer with multiple spinning mills met with Rieter Service specialists to discuss various options for investing in its mills. Rieter recommended carrying out a mill assessment to examine the customer’s mills in detail and check whether there was optimization potential in the components, machine settings or process sequences. The Rieter Service specialists came to the following conclusion: Replacing the existing suction tubes in the compact-spinning machines with an optimized version – the suction tube ECOrized – would reduce the machines’ energy requirements.
The key feature of the suction tube ECOrized is the considerably improved air routing, which makes the suction power more efficient. This reduces the underpressure of the entire compact-spinning machine, while the running behavior and compacting remain consistently good. The Indian customer saves up to 3.5 kWh/h of energy per machine. Since the customer has 14 compact-spinning machines, this means the customer saves INR 3 million every year, which is roughly CHF 36 000. And the yarn quality has remained the same.
Simple Retrofitting and Other Advantages
The suction tube can be retrofitted to the compact-spinning machine families K 44 and K 45, each with up to 1 632 spindles per machine. The retrofit kit contains mainly the tubes, a converter and pressure sensors. Rieter service specialists can retrofit two to three machines every day.