How to Stay Profitable with the Rieter Doffer Maintenance Kit
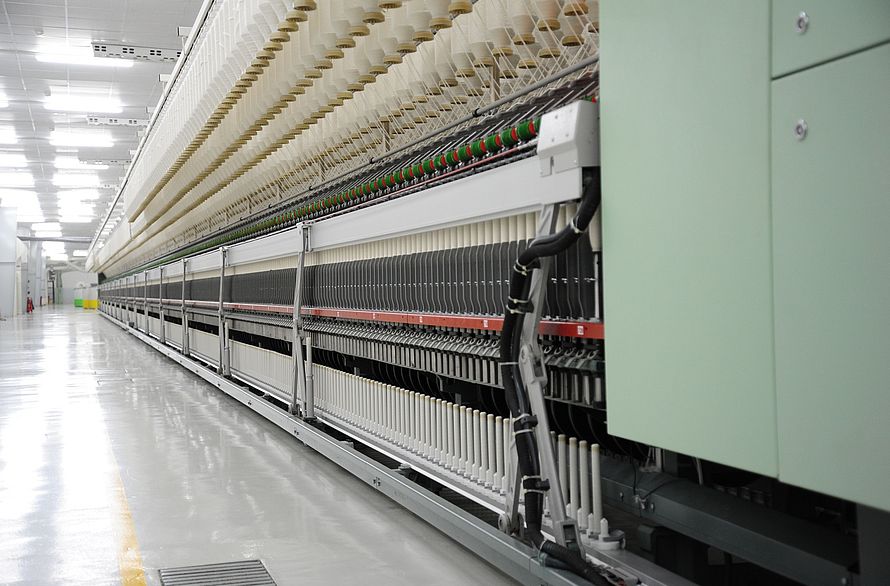
Rieter ring spinning machine with reliable doffing cycle time of 180 seconds.
The doffing cycle time of a ring and compact-spinning machine plays a vital role for higher production efficiency of a spinning mill. Keeping the doffing cycle time at a standard level of 180 seconds positively impacts production by several tons a year. Hence, doffer maintenance is key for consistent productivity to remain profitable and to increase machine lifetime.
The auto doffer process has a significant influence on the productivity and performance of ring and compact-spinning machines. If the doffing cycle time is increased or interrupted due to for instance worn out or broken components, it results in significant production loss. If the doffing cycle time can be kept at its standard level of 180 seconds, it boosts production by several tons per year and increases the machine lifetime.
Impact of the Doffing Cycle Time
Continuous monitoring of the doffer settings and key elements is extremely important for the machine’s efficiency especially in the mid- to long-term. An important component for efficient doffing is the drive belt for the cop transport system SERVOdisc. If the belt is loose or worn, doffing delays can occur. Productivity decreases and production costs increase.
It can become expensive to replace single parts, like profiles or traction strips, while worn SERVOguiding profiles or peg can interrupt the doffing cycle. Furthermore, every single stoppage for the condition-based part replacement will contribute to an increased machine down time.
The graph below shows the productivity loss over time due to increased doffing cycle time. The productivity impact of the doffing cycle time for processing 100% cotton, Ne 30, 1 200 spindles on a Rieter ring spinning machine can be the following: When the doffing cycle time remains at the standard time of 180 seconds, production loss will be zero. If the doffing cycle time extends to additional 30 seconds, which may happen when the doffer is not maintained properly, production will decrease by 1.5 tons per year and machine.
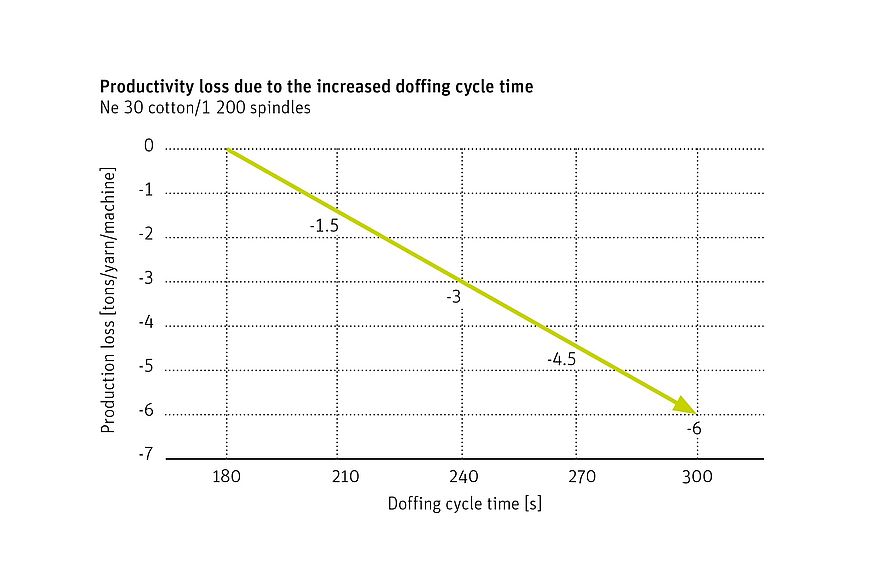
Furthermore, proper doffing has a big effect on the runnability and sustainability of the winding machine. Cops that are not wounded and shaped correctly increase the amount of waste at the winding machine.
Maintenance Helps Increase Machine Lifetime
Rieter field data has shown that a doffer maintenance every eight years ensures a short and reliable doffing cycle and therefore increases the productivity of the spinning machine. As part of the overall ring spinning machine maintenance, it contributes to the extension of the machine lifetime. To reduce its installation time, the doffer maintenance kit will be delivered with pre-assembled parts.
Benefits at a Glance
The doffer maintenance kit was designed to deliver the following benefits for ring and compact-spinning machines.
- Improves productivity
- Keeps doffing cycle time consistently low
- Increases machine lifetime
- Ensures smooth doffing at all times
Customer Testimonial
Customer Name: Poomex Clothing Company, India
Name: Durai Arun, Managing Director
“After the installation of the doffer maintenance kit, the doffing cycle time remains consistent, and the machine efficiency and productivity have increased. We will now focus much more on maintenance of our machines to keep them running with a high performance and to increase their lifetime.”
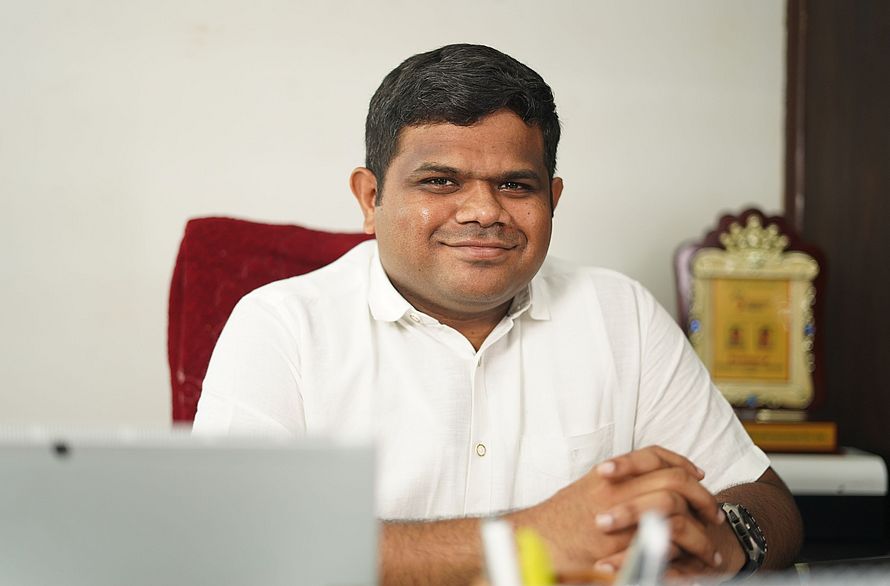