RSB-D 50 at High Delivery Speed with Recycled Raw Material
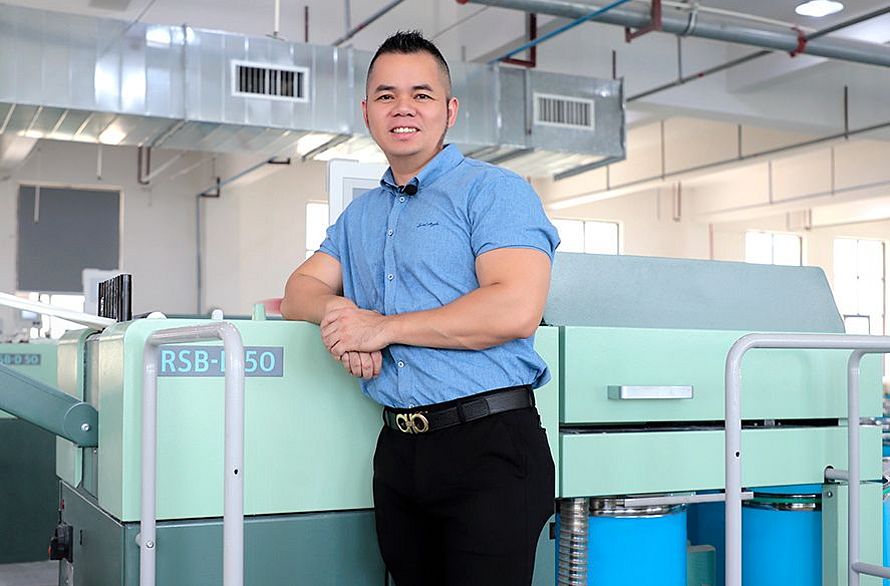
Mr. Huang Jingsheng, Chairman of Wenzhou Luteng, is satisfied with the performance of the RSB-D 50.
Wenzhou Luteng Cotton Spinning Co., Ltd produces rotor yarn from recycled material. The raw material for the yarn consists of fibers from mechanically re-opened polyester-cotton fabric offcuts which are blended with recycled polyester fibers (blending ratio 35/65%). The main end-products are denim fabrics, canvas bag fabrics, mop cloth and curtain fabrics produced from rotor yarn Ne 5 to Ne 10. The seven sets of autoleveler draw frames RSB-D 50 play an important role in the yarn manufacturing process because they ensure high sliver quality and produce with high productivity, also with recycled raw material.
The Challenge
Processing recycled fibers is a challenge for any spinning mill. During the raw material opening process many short fibers and a high amount of dust is created. This can lead to high instability in sliver quality which negatively affects the productivity in downstream processes. The challenge is to get the maximum yield from the given material with the optimum settings and technology. In this context, high expectations are placed on the draw frames because they are a crucial step in the yarn manufacturing process which strongly influence the yarn quality.
The Solution
The RSB-D 50 is a single-head, autoleveler draw frame that has several advantages when it comes to processing recycled material.
- It runs with highest production speed while ensuring consistent quality.
- The RSB-D 50 is equipped with a highly efficient suction system.
- Rieter’s patented sliver guide always guarantees centric guidance of the slivers and ensures consistent sliver quality.
The Customer's Benefits
With a delivery speed of 850 m/min of the RSB-D 50 with recycled raw material, Wenzhou Luteng benefits from highest productivity. While running at this high speed, the machine produces sliver with consistent quality. Thanks to the large top rollers and the lifting cleaning lips, the machine operates with a very low number of lappings, thus achieving maximum productivity. Less sliver breaks in the draw frame lead to less stops in the downstream processes, which reduces the operator workload.
The advanced suction system is a big advantage for the processing of short fibers and dusty material. Trash accumulations on the cleaning lips end up directly in the suction by intermittently lifting the lips. The automatic filter cleaning system keeps the filter screen clean with the help of a wiper. Only on the Rieter draw frame the operator can set the suction intensity easily and quickly on the machine display. Four suction slots in the infeed support the suction concept for an efficient trouble-free 24-hour operation.
In addition, Rieter’s patented sliver guide always guarantees centric guidance of the slivers. This is a prerequisite for high delivery speed and ensures consistent sliver quality. The web width is reproducible and is set by a simple turning of the guide elements. The consistent sliver quality enables excellent yarn quality and also a higher efficiency of the downstream machines.
I am very satisfied with the consistent stability and high productivity of the RSB-D 50. The draw frame is able to process recycled polyester-cotton blends smoothly and trouble-free at 850 m/min. It enables us to spin ordinary recycled raw materials into a high quality, constant end product.Mr. Huang Jingsheng, Chairman of Wenzhou Luteng Cotton Spinning Co., Ltd.
Download
Wenzhou Luteng Cotton Spinning Co., Ltd.
Wenzhou Luteng Cotton Spinning Co., Ltd, located in Cangnan county, Wenzhou city, Zhejiang province, China, was founded in 2018 and is an integrated spinning mill with a focus on producing and processing recycled fibers. This includes the mechanical tearing of used fabrics into single fibers, spinning these recycled fibers into new yarns and finally weaving new fabrics. The spinning mill has a total of 2 580 rotor units with a total capacity of 23 tons per day.