Big Thinking Offers Benefits
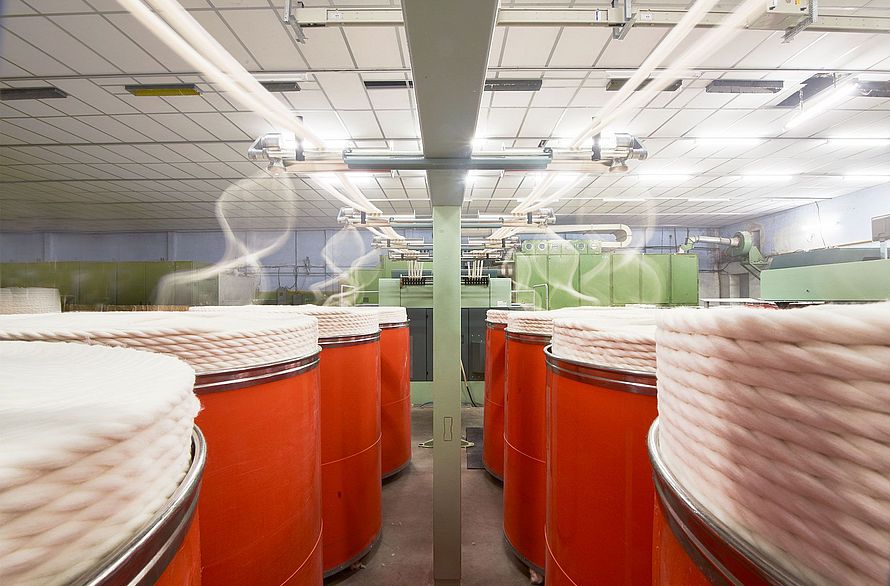
Cans with a diameter of 1 200 mm are the alternative choice in Rieter spinning preparation. They increase the machine efficiency while also reducing personnel requirements and waste. Having fewer sliver piecers also increases the yarn quality.
The new Rieter sliver deposits in cans with a diameter of 1 200 mm offer many benefits, as they reduce operating effort during spinning preparation. The large cans are now also available for cards, draw frames and combers. With this can format, Rieter is offering a solution for the growing challenge of finding operating personnel for spinning mills. In addition, using the cans can help to offset higher labor costs due to increasing wages.
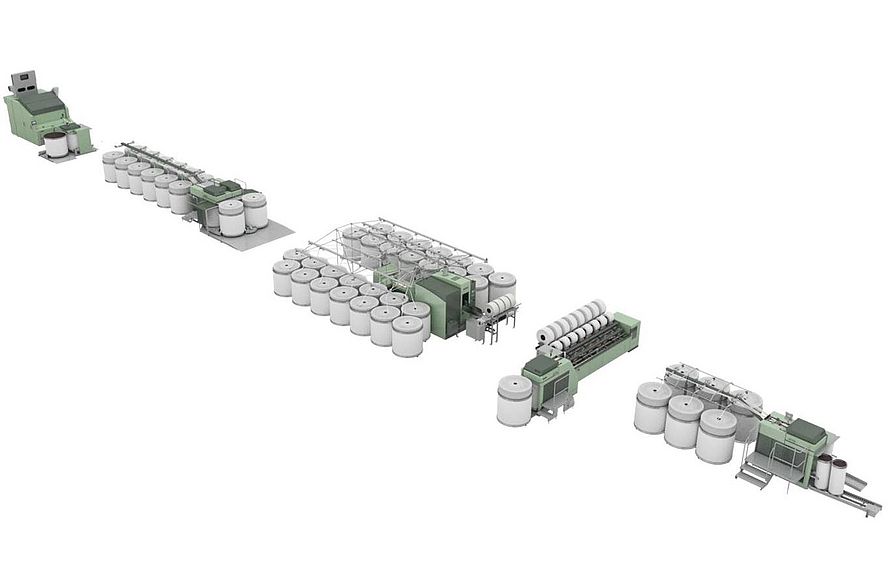
Up to 100 kg Filling Quantity Per Can
Cans measuring 1 200 mm in diameter can hold around 43% more sliver than cans that are 1 000 mm in diameter. With carded cotton, a can height of 1 200 mm equates to a filling weight of 76 kg; for cans that are 1 300 mm high, the filling weight is an impressive 83 kg. With combed fiber material, filling quantities of up to 100 kg can be achieved.
Standstills Significantly Reduced
The higher filling quantities reduce the number of standstills and therefore increase the efficiency of the machines. This is true whether the cans are used at the feed unit or at the delivery unit of the machine. This increased efficiency can be seen most clearly in draw frames without an autoleveler, where the cans can be used both in the feed and in the deposit. Cans with a diameter of 1 200 mm increase the efficiency of the draw frame SB-D 26 by up to 2.5%.
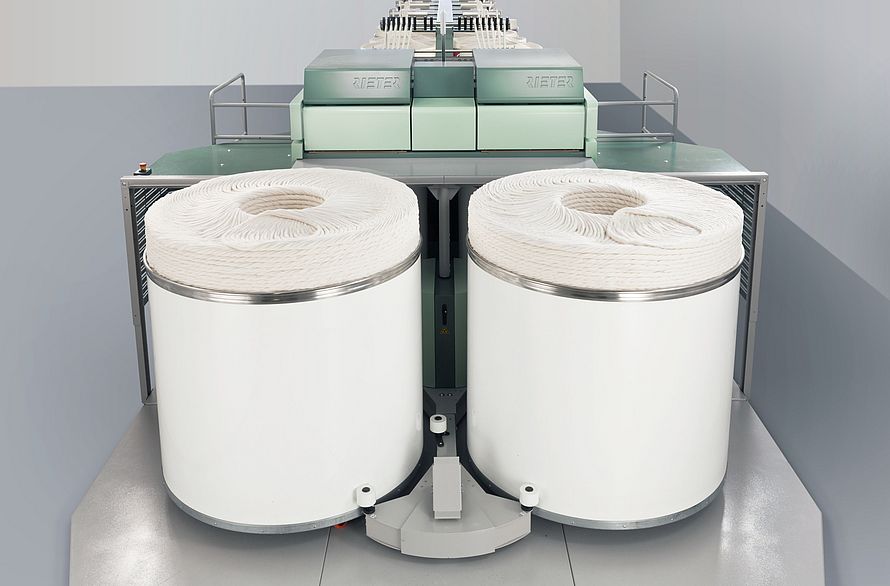
Fewer Can Transports, Fewer Operating Personnel
Having larger filling quantities reduces the number of can transports and changes in the creels of the downstream machines by 30%, meaning fewer operating personnel are required. Smooth-running rollers on the can make it easy to move the cans on the floor of the spinning mill.
An example calculation for a spinning mill with combed ring yarn and a production output of 48 tons per day produces the following results: Using cans measuring 1 200 mm in diameter rather than 1 000 mm in diameter means that one less operator is required per shift – and using 1 200-mm cans instead of 600-mm cans requires almost three fewer operators per shift. The total savings amount to three or eight operators per day.
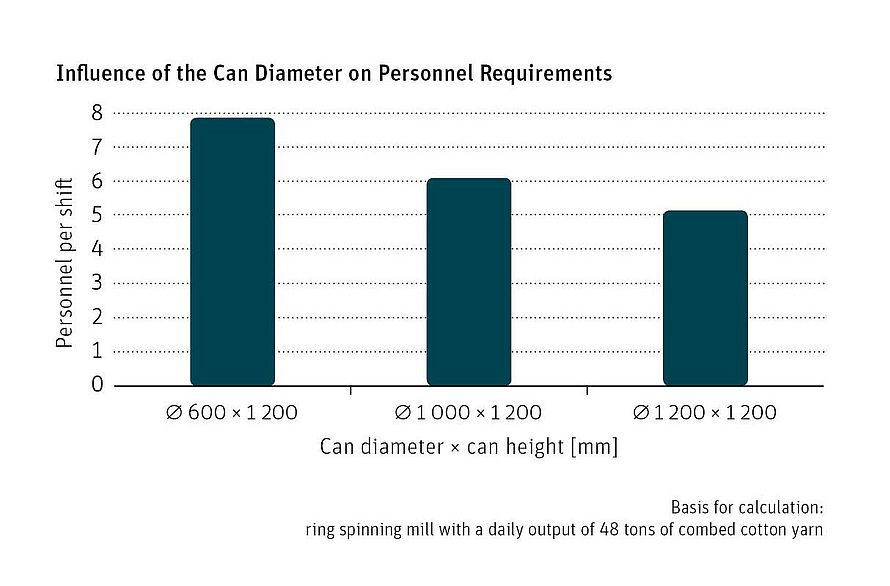
Fewer Sliver Piecers Improve Quality
In the example calculation, there are over 370 000 fewer can transports a year with 1 200-mm cans than with 1 000-mm cans. This affects the transport routes from the cards to the draw frames without autolevelers and to combing preparation, as well as from the combers to the autoleveler draw frames. This consequently saves over 370 000 sliver piecers and results in a correspondingly lower number of defects, which significantly improves the yarn quality.
Every Meter is Processed
The 1 200-mm coiler in the Rieter sliver deposit produces a larger coiling radius in the can. This means that, when the sliver is pulled out in the creel of the downstream machine, the balloon is steadier and the sliver is fed in more gently. Even at high drawing speeds – such as on the combing preparation machine OMEGAlap or on draw frames with a rapid production rate – the cans are completely emptied without interruption. Having larger can diameters therefore also produces less waste.
For cards and draw frames, Rieter also alternatively offers filling systems for can formats with a diameter of 1 000 mm and a height of up to 1 500 mm, which can hold around 25% more material than cans with the regular height of 1 200 mm.