Winding Expertise for Wool Applications
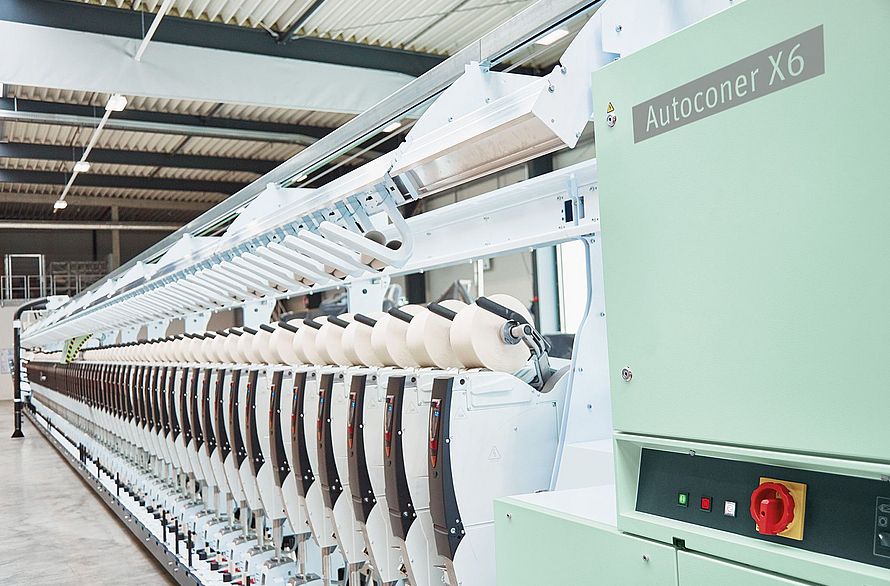
Wool yarns, and thus wool yarn spinning, have a long tradition and have never lost their importance in the textile and fashion industry. Due to its unique and special characteristics, wool fibers are expanding more and more into functional and technical applications.
The spinning and winding of wool fibers and yarns will therefore continue to be an important part of textile industry. And as traditional as the spinning process is, so is the strength of the winding machine Autoconer X6 in winding and processing wool yarns and blends. These include for example also blends of wool, acryl, cashmere, or combinations with elastane filaments. They can be carded, combed, worsted, semi-worsted, single or plied yarn or mule spun cops, and from fine to coarse counts. Customers in approx. 50 countries trust in the Autoconer winding expertise. During ITMA Milan in 2023, the Rieter customer Südwollegroup received the award for the 100 000 Thermosplicer for its plant DaLat Worsted Spinning Co. Ltd. in Vietnam.
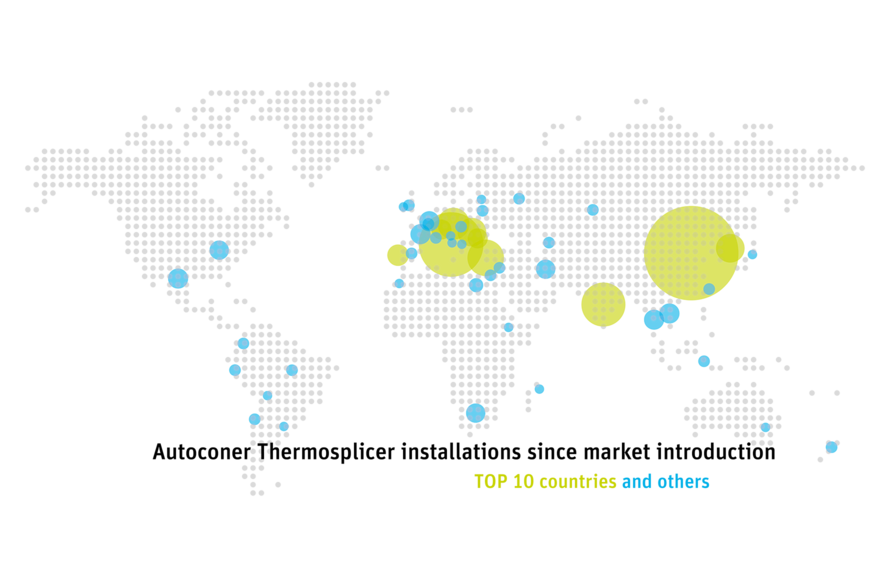
Thermosplicer – Proven and Effective for Wool
The Autoconer was the first winding machine with an integrated Thermosplicer, using the special thermoplastic characteristics of wool and synthetic fibers (such as acryl) as basis for excellent splice results. The central setting of the splice air temperature, and thus the adaptation to the very different temperature behavior of the various fibers and blends is standard for high reproducibility and quality of the splice joints. Thanks to two independent heating systems - prism heating and air splice heating - the correct pre-selected temperature is always used in the splice process, regardless of the number of splice cycles. Switching off the heating systems makes it possible to run the Thermosplicer as a standard splicer. The use of the Quick-change unit makes it as easy as possible to switch between S- and Z-yarn applications without having to dismantle the splicer head. The rapid cooling function for the heating cartridge is a small but important point for operator safety in handling.
Excellent Package Quality for High Downstream Efficiency
Modern sensor technologies, monitoring and autocalibration functions as well as intelligent processes have been developed and integrated into the Autoconer to be more gentle, more efficient, more precise, and more flexible. This fulfills the increasing demands of the wool business regarding quality, flexibility, sustainability, and operator independency.
Process-optimized packages are a key point for the Autoconer. Thanks to an individual, software-controlled package build-up, Preci FX supplies package formats optimally and flexibly adapted to the requirements of the respective downstream processing, by touch of a button. The round edge design for dye packages is groundbreaking for excellent quality in dyeing. It can be easily switched between packages with traverse of 3”, 4” or 6”, using only an adapter, to offer flexibly the right format for twisting packages. Autotense FX, Variotense FX, Propack FX and Variopack FX efficiently prevent the package flanks from bulging-out when winding elastic materials such as wool or wool/elastane yarns. A package build-up with straight package flanks is ensured for easy handling and creeling in downstream processing.
Highest Flexibility, Reliability and Raw Material Yield
Automation with the Autoconer X6 is not only effective and highly flexible, it also ensures maximum process reliability. RFID-technology with complete material tracking is the standard. The new Color Check additionally monitors the correct allocation of cop and Smarttray to avoid material and lot mix-up. This guarantee is essential for demanding wool yarn processing to prevent quality loss and waste of valuable yarns.
Q-Package, a feature for intelligent feed material handling and alarm cop management on the Autoconer, type D, reduces the manual setup effort to a minimum and saves valuable resources. The machine can perform the feed material change in the shortest possible time, or it can do so intelligently to produce a maximum number of full packages with highest utilization of the feed material. This is advantageous both for highest flexibility and for maximum use of resources in the segment of high-quality wool yarn processing. In linked systems (type V) the online quality monitoring system SPID ensures the high-quality standard of the wool fiber processing. This is available as standard function in the Autoconer X6, either as a direct link, Multilink or in combination as link with integrated steaming process.

Customers can continue to rely on Rieter’s excellent technological experience, state-of-the art machine technology with a lot of further beneficial features as well as sales and service support in the processing of wool yarns and their blends.
Südwollegroup, the world's largest manufacturer of worsted yarns, has relied on the Autoconer for many decades. For us, the Autoconer is the benchmark for winding machines in the wool yarn spinning sector, and therefore the first choice for us as the market leader. Its Thermosplicer is the most proven system for excellent splice joints on the market. New features for higher package quality were developed with each machine generation, for example Autotense FX, Preci FX, Ecopack FX. This enabled us to continuously improve our product quality. It is a reliable partnership at the highest technical and technological level.Jürgen Schönberger, VGM of the Südwollegroup China