Reducing the Carbon Footprint
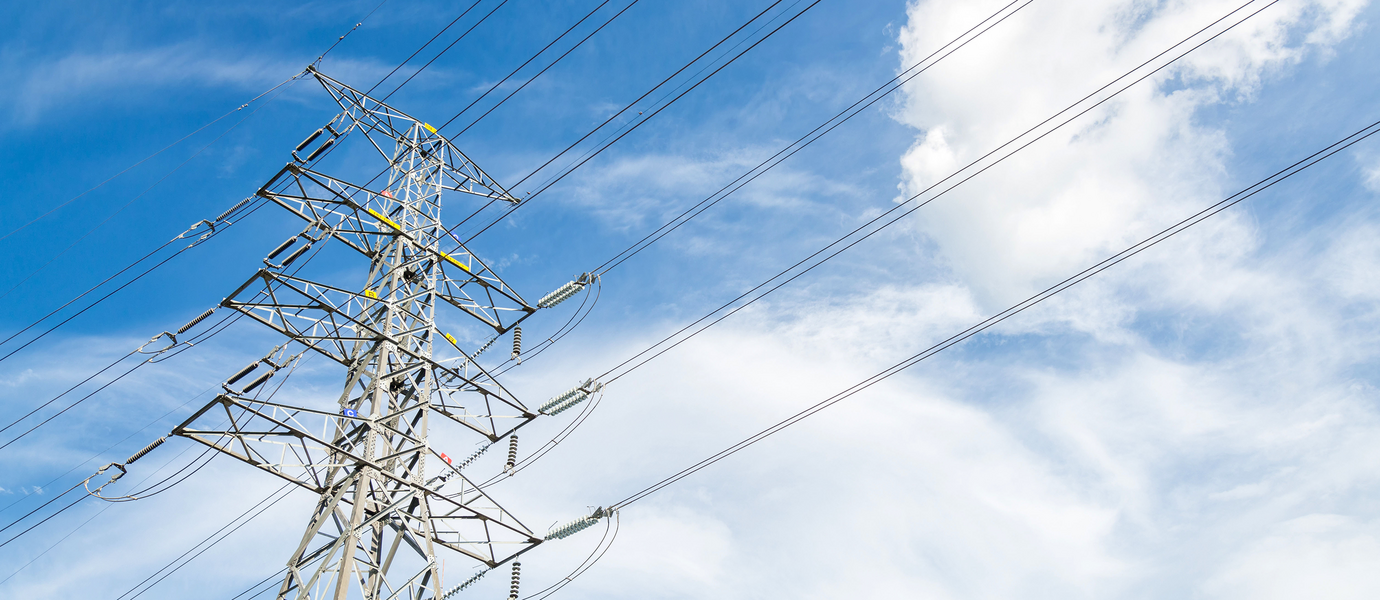
The fashion industry is responsible for a considerable proportion of global CO2 emissions. Estimates suggest that it accounts for 4 to 7% of global greenhouse gas emissions. As part of the fashion industry, the textile industry is also in focus. Major fashion brands are increasingly demanding transparency regarding the CO2 footprint of their goods. This requirement has increased demand for yarn produced in an environmentally friendly way. Rieter spinning systems, particularly its energy- efficient end spinning machines, make a significant contribution to reducing the carbon footprint.
In addition to selecting sustainable fiber material and using renewable energy sources, energy-efficient machines are an important tool of the textile industry for reducing CO2 emissions. Rieter offers an energy-efficient portfolio for all spinning systems. This applies to every single machine in the process, with the end spinning machines (ring, compact-, rotor or air-jet spinning machines) offering the greatest potential for energy savings. Depending on the procedure, the end spinning machines use 63 to 79% of the energy across the entire spinning process. The finer the yarn, the more energy required. The energy saved by the end spinning machine is therefore even more important. Rieter thus focuses on these machines and, in particular, invests in energy-saving technologies and developments. Every energy saving, however small, clearly pays off.
G 38 with COMPACTdrum uses 15% less energy
Because of their technology, ring and compact-spinning machines consume a high amount of energy per kilogram of yarn compared to rotor and air-jet spinning. Using energy-efficient machines is therefore even more important. Energy-saving motors and an innovative suction system mean that the ring spinning machine G 38 with a fully electronic drafting system meets all requirements for efficient yarn production. In combination with the compacting device COMPACTdrum, the G 38 uses up to 15% less energy compared to the compact spinning machine of a competitor.
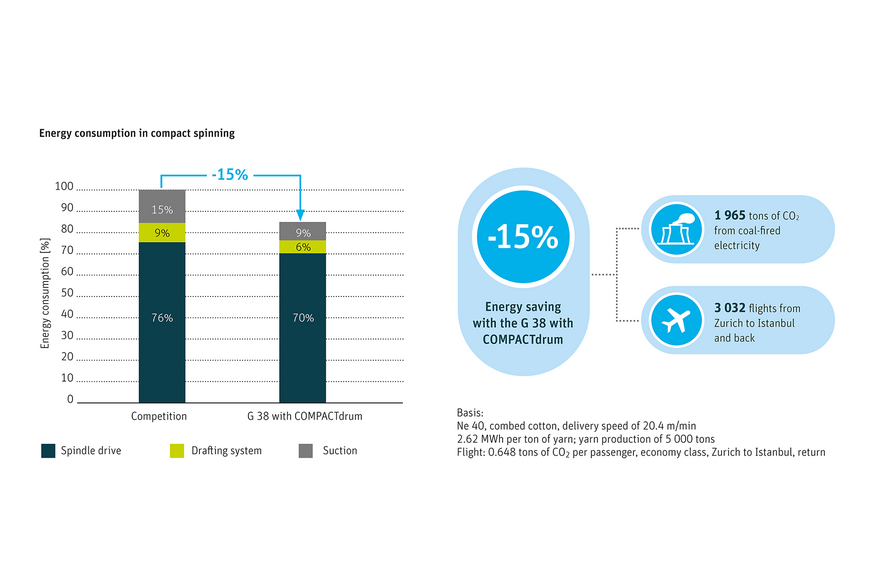
5% lower energy consumption with the R 70
Rotor spinning is the spinning technology with the lowest energy consumption per kilogram of yarn produced. The fully automatic rotor spinning machine R 70 also has the lowest energy consumption compared to competitor machines. The efficient suction of the machine and the modern drives generate energy savings of 5% in total.
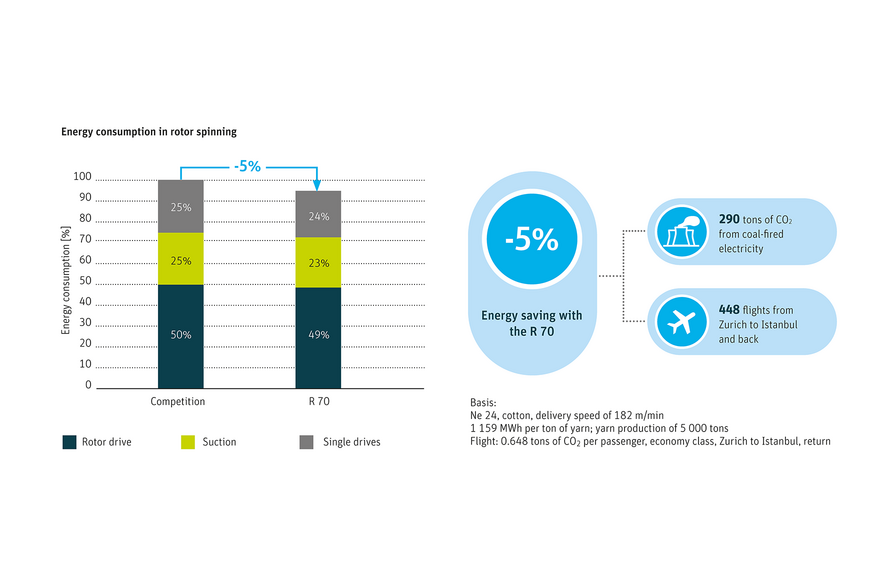
J 26 uses 15% less energy
Two different types of energy are required for air-jet spinning: electrical energy for the drives and suction system, and compressed air for fiber twisting during yarn formation. The drive concept of the J 26 is based entirely on individual drives. In total, the air-jet spinning machine J 26 uses around 15% less energy per spinning unit than the next-best competitor machine.
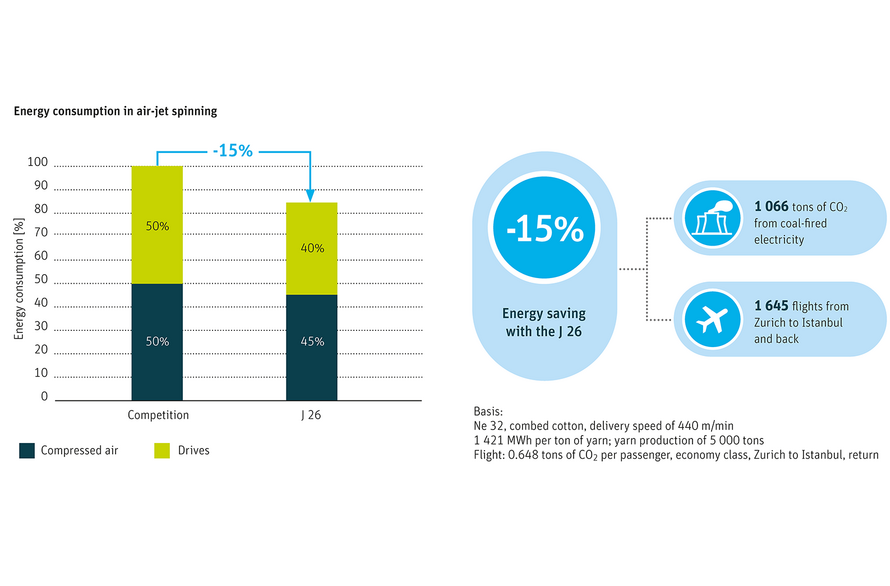
Rieter systems considerably reduce the energy consumption of yarn production. Rieter is therefore making an important contribution to reducing CO2 emissions and strengthens the competitiveness of spinning mills, as they can meet the increasing demand for yarns produced in an environmentally friendly way.