New Perspectives with the Autoconer X6
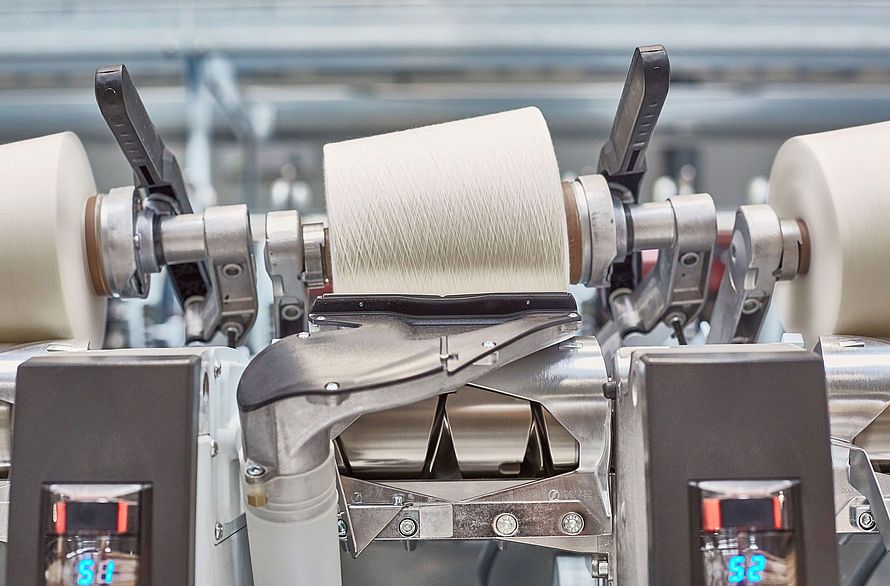
Energy efficiency is the key to decarbonizing yarn production. With the automatic winding machine Autoconer X6, Rieter has added another all-star performer to its energy-efficient technology portfolio, while at the same time contributing to maximum resource utilization. Integrating the automatic winding machine into the Rieter ring and compact-spinning system also paves the way for further efficiency increases, even in downstream process stages of the textile value chain. Digitization and artificial intelligence open up new prospects for the future.
Some process steps in the textile value chain consume the scarce resource that is water and require the use of chemicals on a large scale. These include, for example, the production of synthetic fibers and dyeing. When spinning fibers into yarn, the electrical energy required to operate the machines determines the environmental footprint, especially if it comes from fossil sources.
Rieter’s ring and compact-spinning system sets the industry benchmark for energy consumption and thus for CO2 emissions in yarn production. Assuming that the required electricity is generated from coal, the production of one ton of yarn with a Rieter system releases about one ton of CO2. The Rieter system emits about 10% less emissions than competitor systems.
Precision Creates Advantages
As the final process stage in ring and compact spinning, the winding machine accounts for around 14% of energy consumption in the spinning mill and is therefore the focus of efforts to reduce energy consumption. Generating the vacuum is one of the processes that consume the most energy in the winding process. A vacuum is necessary to enable reliable yarn detection and gripping during all cycle operations on the Autoconer. Reliable yarn detection and gripping means high productivity, resource conservation, and quality-assured package handling. The Autoconer operates at a lower vacuum than competitor machines thanks to sensory monitoring and control. The resulting advantages in energy consumption over competitor machines are significant and range from 7% to 70%, depending on the competitor, machine type, and the number of winding units and cycles.
When it comes to minimizing material consumption, precision in yarn cleaning is the key. During yarn cleaning, faults are removed and yarn ends are reconnected using splicing technology. Eliminating a defect, including splicing, takes only five to six seconds. Then the splice optics are checked to ensure that they meet the quality requirements. If the spliced yarn is too thick or too thin, it is spliced again.
The new open prism splicing technology improves the optics of the splice joint with high precision and uniformity. This means fewer repeats and consequently less yarn waste.
Positive Impact on Downstream Process Stages
One example of the increase in efficiency in downstream process stages is the production of dyeing packages on the Autoconer X6. The package building process has a significant influence on the dyeing process and thus on the consumption of water, dye chemicals, energy consumption and the quality of the dyeing results. With the Preci FX drumless yarn traversing system, the Autoconer took on a pioneering role at an early stage and for the first time specifically optimized the design of the dyeing packages. The combination of Preci FX and the yarn tension control system Autotense FX allows to produce the exact uniform package density as required by the dyer. This is a prerequisite for uniform dyeing results in the first dyeing cycle. This conserves resources and lowers costs.
New Prospects Thanks to Artificial Intelligence
The Autoconer X6 is integrated into the Rieter ring and compact-spinning system via ESSENTIAL, Rieter’s digital platform for spinning mill control. Integration opens up the potential for enhanced transparency and optimization from bale to package. Not only will it be possible to detect relevant deviations in production even faster and more comprehensively, but it will also be possible to identify and eliminate the causes across the entire process. This takes place based on rules and thresholds as well as the evaluation of machine events throughout the process. In this way, ESSENTIAL maps the expert knowledge of spinning operations in the form of artificial intelligence and creates the basis for a learning system. The use of artificial intelligence will make a significant contribution to automation and process optimization, and thereby advance sustainability in the textile industry. To further develop expertise in the field of Industrial Artificial Intelligence, Rieter and the Johann Jacob Rieter Foundation are funding a professorship at the ZHAW School of Engineering in Winterthur (Switzerland).