After Sales Services
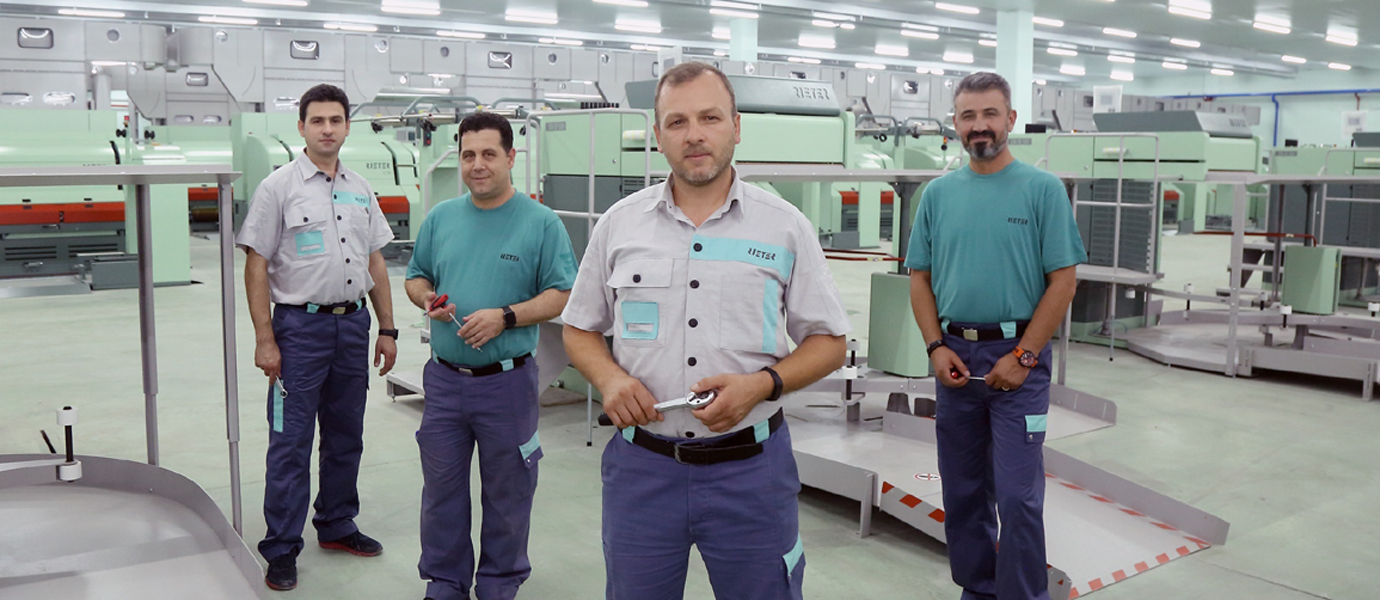
After Sales Services help customers get the most out of their products and systems so they can stay ahead of the competition. From Performance Optimization Services through to retrofits, original parts, upgrades, and in-depth expertise, Rieter is a partner for the long run. Embracing these services turns into a competitive advantage for mills and helps support environmental sustainability.
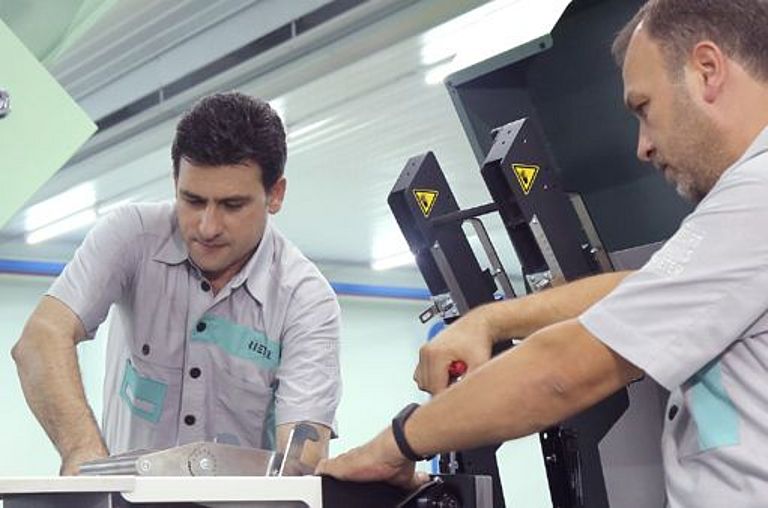
Mill Assessments boost efficiency
Performance Optimization Services support in boosting mill efficiency and reduce yarn production costs, giving customers a competitive advantage and contributing to the sustainability of a spinning mill. Customers benefit from improved processes and expert recommendations. After assessment, Rieter provides a tailor-made report drawn from on-site data collection and analyses, as well as a customized solution concept. This concept includes process optimization and reorganization, wear and tear parts exchange, conversion recommendations and more.
Buhler, the leading supplier of fine yarns, with headquarters in Jefferson, Georgia, USA worked with Rieter to optimize its spinning mill. As a result, mill productivity and yarn quality were massively improved, while considerable raw material savings were achieved. Production costs were reduced and employee skills were enhanced. The reduced production costs mean that the investment in mill assessment, technology components and machine upgrades will be paid back in less than 18 months, giving Buhler scope for further investments.
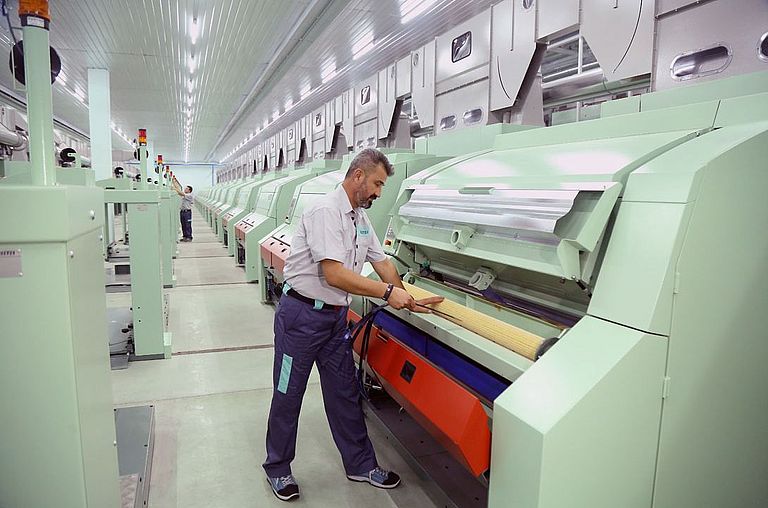
Preventive maintenance packages increase machine uptime
Rieter machines are renowned for their outstanding performance. But even the best equipment needs replacement parts now and then. To use resources efficiently and be competitive, yarn producers must minimize production stops. One planned maintenance overhaul operation is less costly than several small last minute production stoppages. Customers benefit from quick and easy access to original quality parts, at a considerably lower cost thanks to attractive package prices. The Rieter Preventive Maintenance Packages help spinners stay one step ahead of competition by maximizing uptime and use resources economically.
Over the years, Rieter specialists have analyzed the equipment from A to Z and identified several performance-critical parts that need to be replaced after a certain period. This enables customers to easily plan their preventive maintenance and order the parts in one package, right when they need them.
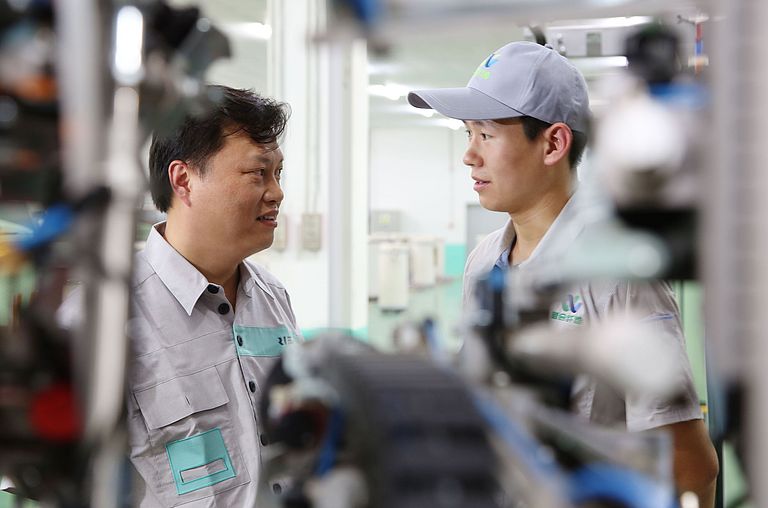
Training maximizes mill performance
Tailored training for mill personnel ensures sustainable production through high machine performance. Training not only improves skills, it also motivates employees to contribute to a company’s goals to improve quality, optimize productivity, increase safety and much more. This ensures a higher return of investment based on efficient use of resources. Training can take place in one of Rieter’s training centers or directly at the customer’s mill.
A sample calculation demonstrates that investments in personnel training are worthwhile. Investments in maintenance skills increased machine efficiency by 1.2%. The manufacturing cost for a Turkish customer was consequently reduced by 0.054 CHF per kilogram produced yarn. This was based on a ring yarn production of 100% cotton combed, Ne 60, 520 kg/h.
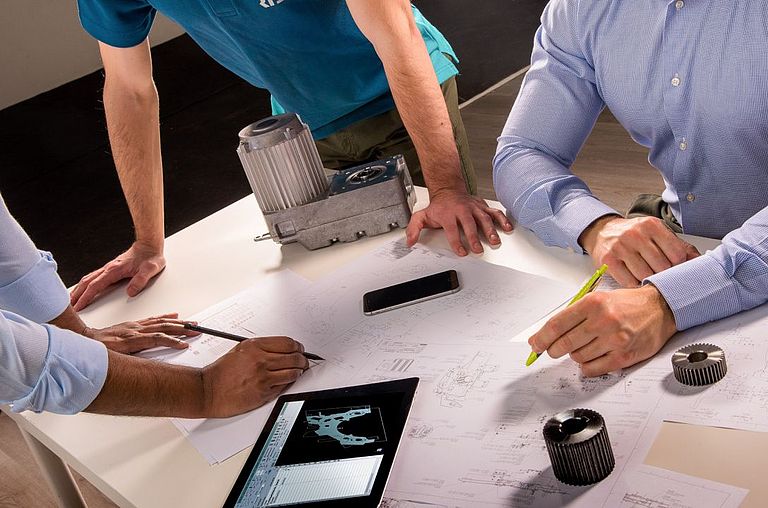
Efficiency thanks to Engineered Solutions
After several years of operation, machines no longer fulfill present day requirements. Every little boost to recover their initial productivity contributes to the service life of the machine thereby supporting company sustainability. Rieter provides a wide range of solutions to restore spinning mill equipment to its best levels and beyond. The following two examples show how customers and the environment profit from this kind of modernization.
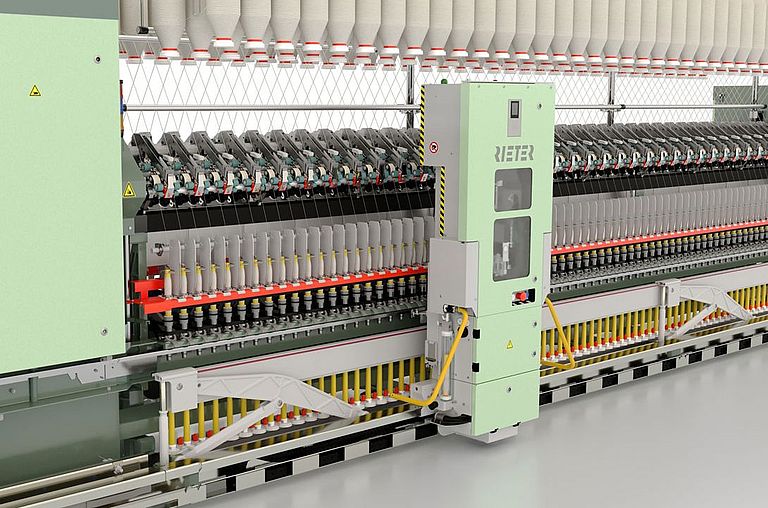
ROBOspin increases machine availability
ROBOspin is the piecing robot for Rieter ring and compact-spinning machines and is offered for new machines as well for the installed base as retrofit. It automates the piecing of ends down that occurs during spinning or after doffing thus increasing machine availability and productivity. Personnel can direct their attention elsewhere, thus improving overall efficiency.
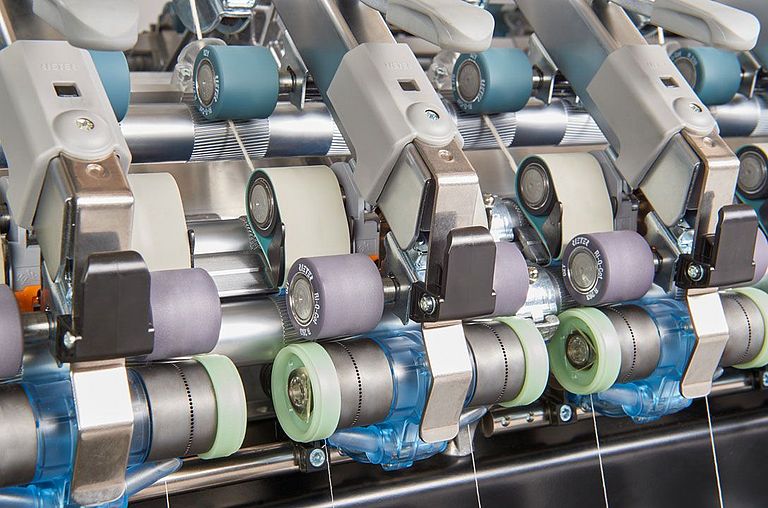
Modernization in compact spinning
The compacting device COMPACTdrum for Rieter ring spinning machines is a great option for spinning compact yarns. It is simple to install and remove and offers higher flexibility with easy switching between ring and compact yarn. With COMPACTdrum, customers can profit either from very low hairiness and high yarn strength. Alternatively they can benefit from the full potential of lower grade raw material for a standard yarn quality. The durable technology components ensure that the yarn quality stays consistently high in the long term. In addition, COMPACTdrum features a detect function that permanently monitors the compacting process. This creates consistently fully compacted yarn and reduces personnel requirements. High flexibility and low energy costs combined with very low production costs maximize resource efficiency.
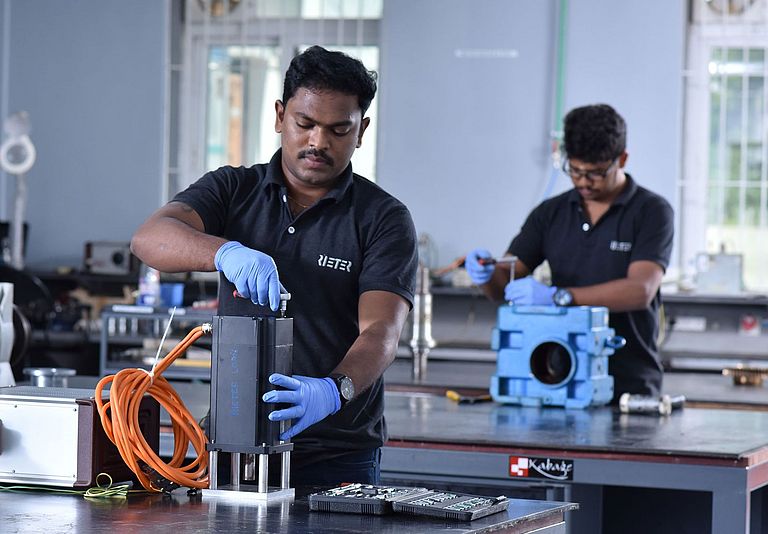
Extended lifetime with repair services
To optimize the performance of the spinning mill, Rieter also offers electronic and mechanical repair services as well as preventive services. All contribute to sustainability by prolonging the life cycle of products. Repair services provide reliable, long-lasting and cost-efficient solutions – quickly and systematically – to lower the risk of a breakdown. With certified experts across 24 repair service centers around the globe, Rieter provides as-good-as-new repairs that extend the lifetime of textile machinery.