Digitization
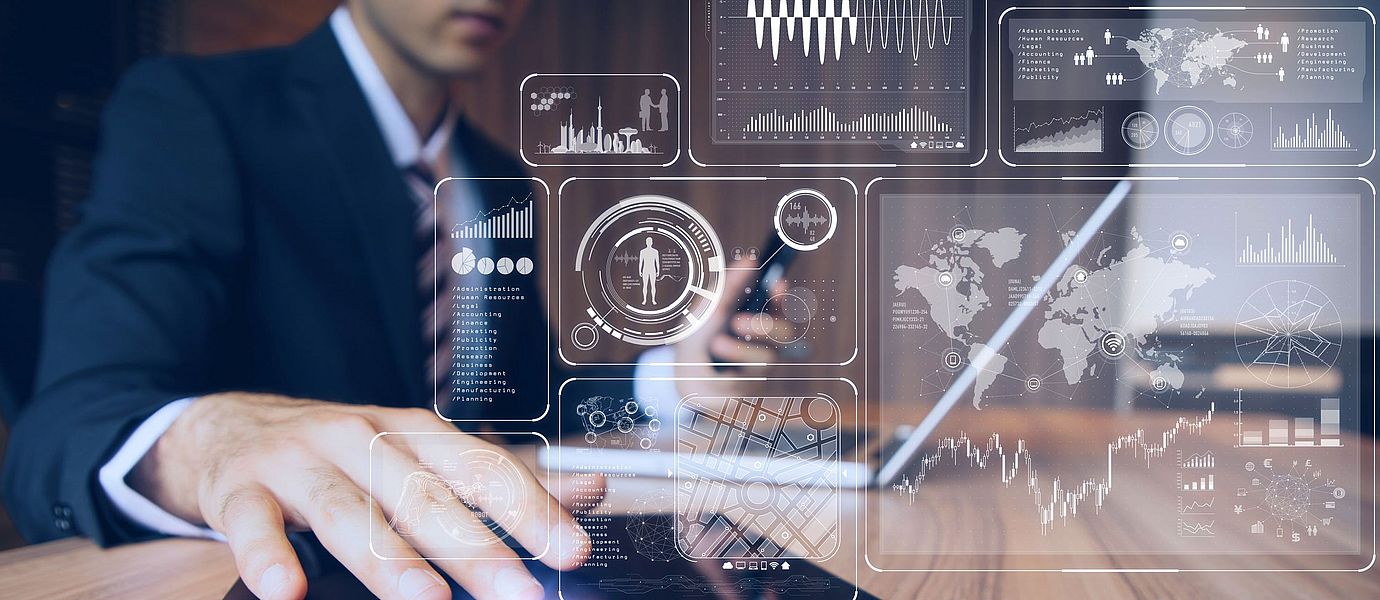
The conventional way of running a spinning mill is a complex and time-consuming enterprise. It means coordinating with lots of different teams, collecting information from various sources, and conducting lengthy meetings to weigh all the options. The all-in-one mill management system ESSENTIAL changes all this. ESSENTIAL shows every key performance indicator in one single view, connecting all machines, auxiliaries, and operational management systems. Now spinners can monitor the entire process at a glance and make decisions quickly and effectively. And it gets even better: ESSENTIAL makes it easy for spinners to maximize efficiency and minimize their environmental impact.
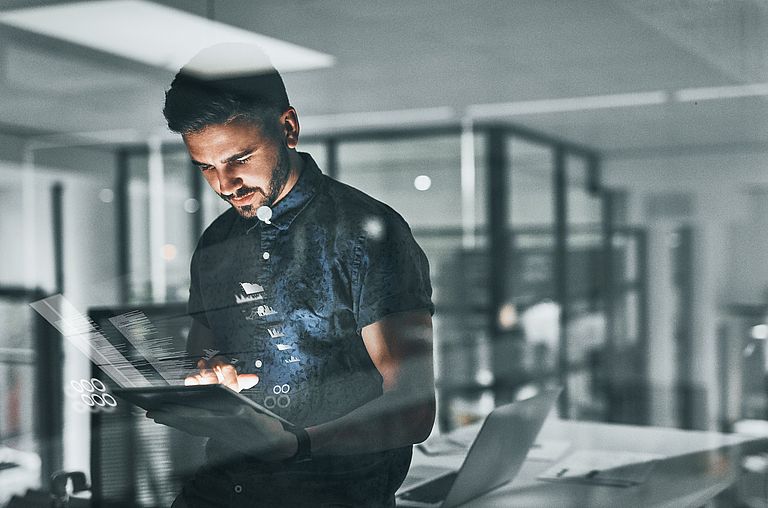
Taking the right measures
ESSENTIALmonitor, one of the available ESSENTIAL modules, provides clearly organized data from the entire spinning process centrally. This helps to collect all relevant information, identify weaknesses, and manage personnel in the most focused way. The specific and continuous stream of data on production, energy and quality enables managers to react quickly and effectively when issues arise. This increases the productivity of spinning mills and allows efficient use of resources.
Achieving production targets at any time
The “Estimated Production” function is part of ESSENTIALmonitor and compares the spinning mill’s actual production with its current benchmark. Managers receive an alert if actual production does not meet the preset values. Thanks to user-friendly navigation, operating personnel can access deeper levels of information step by step. They can detect which machines, articles or machine groups are underperforming. Deviations can be remedied during their shift instead of waiting until after the end of it.
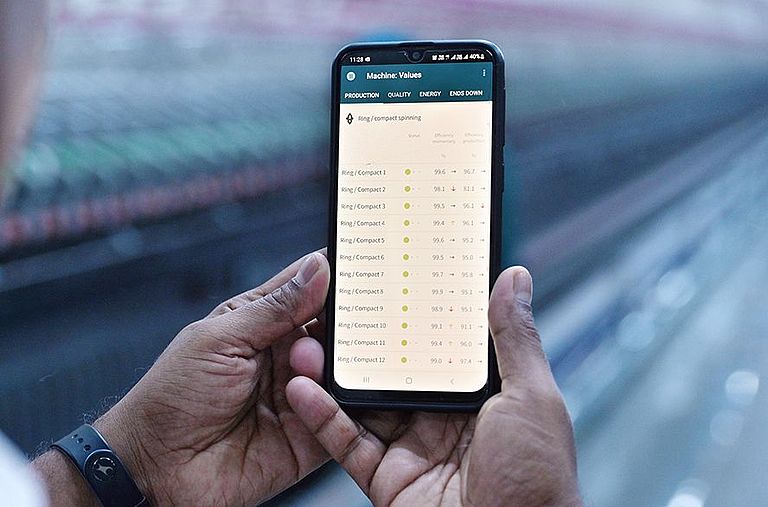
A comprehensive picture
ESSENTIALoptimize is connecting the dots in the entire spinning mill. By providing a comprehensive picture of process deviations, e.g. quality faults, the system makes it possible to link machine performance and events. This revolutionizes process optimization in spinning and saves valuable raw material.
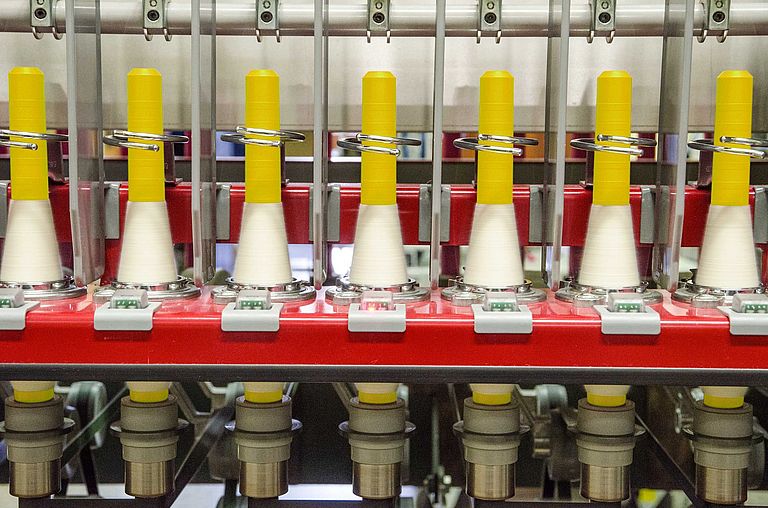
Increasing productivity with ISM
The Individual Spindle Monitoring system (ISM) for ring and compact-spinning machines allows the permanent monitoring of every single spindle. LED at each spinning position detect ends down which are visualized in ESSENTIAL. Detailed evaluations are possible and weak points are indicated. This optimizes operator guidance and increases machine efficiency.
Saving energy resources
ESSENTIALmonitor offers the possibility to track energy consumption throughout the spinning process. The available data can be drilled down from mill level to machine level. One valuable figure which can be checked is the energy consumption per kilogram of produced yarn. Machines with inefficient energy behavior can be easily identified. If a predefined threshold is exceeded, a real-time trigger is sent both via SMS and email. The alarm includes clear actions, assignments and status reports so operatoring personnel know how to optimize the spinning mill’s energy consumption, saving precious energy.
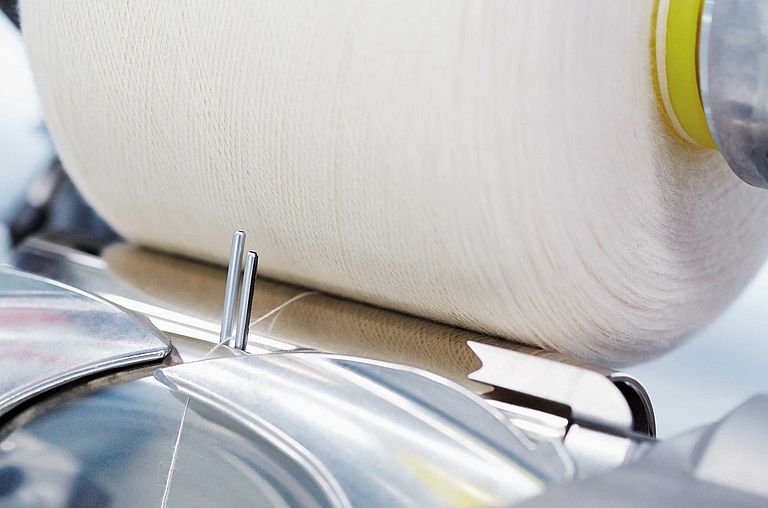
Optimal raw material usage
The continuous monitoring of all available online quality data helps to save raw material. Exceptions to the predefined threshold values are indicated on specific machines. Defects are detected directly during the spinning process. This prevents the production of faulty material and therefore saves valuable raw material.